- 1,234
- 2,246
- 113
- Location
- Wenatchee, WA
Given the amount of noise in the cab of these trucks and wanting to be able to talk to the person next to me without yelling I resolved to install an intercom. I looked and asked around the forum and other places but did not net much responses for what folks have done in their soft top cabs for a hard-mounted intercom so I decided to design one from scratch. The idea I had was to mount something to the tubes spanning across the top back of the cab so it would kinda be overhead but also would be behind the passengers. In addition to the intercom I thought this panel would be a good place for an interior light to shine down on the floor & dash when needed. My truck is actually an M813, but since it seems more M35's have soft tops than 5 tons and since they share a common cab/roof anyway I thought this would be a good place for the thread.
To start with I ordered a 4-person VIC-1 system from Recodefense (very nice stuff by the way) and once that arrived I had something tangible to look at and see if they would fit without smacking the riders in the head. Looks like there will be plenty of room. The 4-person system consists of (1) AM-1780 amplifier and (4) C-2298 crew control boxes - the cables to connect and power everything are not included so it's off to online auction sites to gather those up.
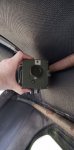
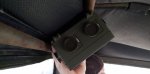
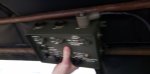
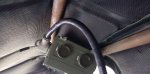
It took several weeks to gather all the cables and I even got one from Santa Claus during Christmas break! Now that I have the cables I can do some CAD work (cardboard-aided design) and play musical boxes to arrange them to miss everybody's head.
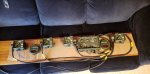
My brother and I clamped this piece of cardboard to the roof support tubes and outlined our heads while we leaned back in each of the 3 places a full grown person would sit. The way the cables connect (they are indexed) and the way they bend actually dictated how far apart the boxes would be spaced. It looked even enough so I decided not to argue with the cables. They had a natural way they wanted to lay and didn't like being forced into a different position. My buddy donated a pair of M-38 taillight covers to the project so I will make good use of them for the courtesy lights! Up next is to see what the digital CAD is going to tell us about the details of the panel and installation.
I don't have much time these days for long-winded write-ups so I'll update this as I go. Tag along to see how it will all come together (or fail)!...
To start with I ordered a 4-person VIC-1 system from Recodefense (very nice stuff by the way) and once that arrived I had something tangible to look at and see if they would fit without smacking the riders in the head. Looks like there will be plenty of room. The 4-person system consists of (1) AM-1780 amplifier and (4) C-2298 crew control boxes - the cables to connect and power everything are not included so it's off to online auction sites to gather those up.
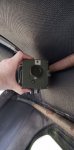
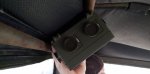
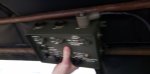
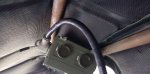
It took several weeks to gather all the cables and I even got one from Santa Claus during Christmas break! Now that I have the cables I can do some CAD work (cardboard-aided design) and play musical boxes to arrange them to miss everybody's head.
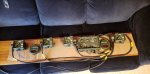
My brother and I clamped this piece of cardboard to the roof support tubes and outlined our heads while we leaned back in each of the 3 places a full grown person would sit. The way the cables connect (they are indexed) and the way they bend actually dictated how far apart the boxes would be spaced. It looked even enough so I decided not to argue with the cables. They had a natural way they wanted to lay and didn't like being forced into a different position. My buddy donated a pair of M-38 taillight covers to the project so I will make good use of them for the courtesy lights! Up next is to see what the digital CAD is going to tell us about the details of the panel and installation.
I don't have much time these days for long-winded write-ups so I'll update this as I go. Tag along to see how it will all come together (or fail)!...
Last edited: