- 268
- 483
- 63
- Location
- Indianapolis, Indiana
I wanted to clarify some additional information on adapting a Cummins 6BT engine to the Spicer 3053a transmission in an M35A2. This came up in another thread, so to avoid derailing that thread I started this new one. A link to the original thread is below.
@gringeltaube posted an excellent diagram for this scenario, which I have copied below.
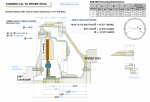
When I had taken some (very rough) measurements a long time ago, I didn't remember things working out as well as the diagram shows. I remembered the splines not reaching the flat surface of the flywheel. The thread above compelled me to go measure parts out in my shop. Here's what I found.
My flywheel housing (3921296) measured the same as the diagram.
My SAE2 to SAE3 adapter ring is 14 mm thick, 2 mm thicker than shown (it is not a military part). I think I could have this milled down to 12 mm and gain 2 mm (or 11.5 to gain 2.5 if necessary), and there is room under the short socket head capscrews to not have them interfere with the transmission. Relatively easy improvement.
My (spare) Spicer 3053a dimensions matched the diagram as well. Not surprising since they should all be the same, but you never know.
What was different for me was the flywheel. Mine (3921264) is only 33 mm thick, 5 mm in the wrong direction. @gringeltaube is there any chance you know the part number of the flywheel you took these measurements from? I'm confident that mine has not been resurfaced down a full 5 mm, and I suspect it has never been resurfaced at all, although it desperately needs it now. If I could find the thicker flywheel, it would move things in the right direction considerably.
I'd also like to ask about the 7 mm shortening of the flywheel housing. Did you do this on an aluminum housing? The thread depth of the SAE #2 mounting pattern are plenty deep to still have thread engagement with 7 mm less depth. I'm somewhat worried about the strength of the rear face with that much material missing - it goes from about 17 mm to only 10 mm. Maybe that is still plenty, but it feels like a big change. I drew a line on my flywheel housing to show the 7 mm distance.
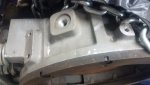
So, if I assembled everything with my parts like they are today, I would have the splined input shaft short of the flywheel face by ~2.29 mm. If I shortened the SAE2 to SAE3 adapter ring by 2.5 mm, I could get it close to flush after resurfacing the flywheel, and not have to modify the flywheel housing. Is that good enough if a sufficient pilot bearing / bushing adapter is made?
Any assistance you can give is genuinely appreciated. I'd like to get everything ready for when I do get around to performing this conversion. I'm just not quite there yet.
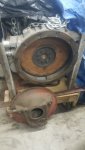
Cummins M35A2 starter question
Putting together a list of notes for all the things I'll need to do a 12 valve swap. I've been watching tactical repair on youtube to get as much as I can, but still have a few questions. So I'll need a 24 volt 28MT 10 tooth bendix gear starter. I've found them but with different pinion...
www.steelsoldiers.com
@gringeltaube posted an excellent diagram for this scenario, which I have copied below.
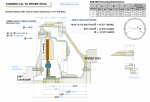
When I had taken some (very rough) measurements a long time ago, I didn't remember things working out as well as the diagram shows. I remembered the splines not reaching the flat surface of the flywheel. The thread above compelled me to go measure parts out in my shop. Here's what I found.
My flywheel housing (3921296) measured the same as the diagram.
My SAE2 to SAE3 adapter ring is 14 mm thick, 2 mm thicker than shown (it is not a military part). I think I could have this milled down to 12 mm and gain 2 mm (or 11.5 to gain 2.5 if necessary), and there is room under the short socket head capscrews to not have them interfere with the transmission. Relatively easy improvement.
My (spare) Spicer 3053a dimensions matched the diagram as well. Not surprising since they should all be the same, but you never know.
What was different for me was the flywheel. Mine (3921264) is only 33 mm thick, 5 mm in the wrong direction. @gringeltaube is there any chance you know the part number of the flywheel you took these measurements from? I'm confident that mine has not been resurfaced down a full 5 mm, and I suspect it has never been resurfaced at all, although it desperately needs it now. If I could find the thicker flywheel, it would move things in the right direction considerably.
I'd also like to ask about the 7 mm shortening of the flywheel housing. Did you do this on an aluminum housing? The thread depth of the SAE #2 mounting pattern are plenty deep to still have thread engagement with 7 mm less depth. I'm somewhat worried about the strength of the rear face with that much material missing - it goes from about 17 mm to only 10 mm. Maybe that is still plenty, but it feels like a big change. I drew a line on my flywheel housing to show the 7 mm distance.
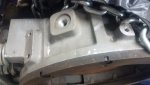
So, if I assembled everything with my parts like they are today, I would have the splined input shaft short of the flywheel face by ~2.29 mm. If I shortened the SAE2 to SAE3 adapter ring by 2.5 mm, I could get it close to flush after resurfacing the flywheel, and not have to modify the flywheel housing. Is that good enough if a sufficient pilot bearing / bushing adapter is made?
Any assistance you can give is genuinely appreciated. I'd like to get everything ready for when I do get around to performing this conversion. I'm just not quite there yet.
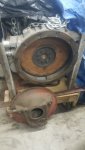