T_F_E
New member
- 207
- 0
- 0
- Location
- Metaline Falls, Washington
When I went to start the turbo project on my 84 cucv blazer I saw that there were many questions on how to turbo a 6.2, but no way of showing how to do it. So I decided to document my process and create a pictorial tutorial. I will probably add more as I remember more. Keep in mind I am 17 years old and I am just a back yard mechanic.
Materials
Borg-Warner GM-x series turbo
Intake manifold
Upper intake manifold
Drivers side exhaust manifold
Two exhuast manifold gaskets for 6.2 diesel motor.
Five 90mm 10m x1.5 studs
Five 10m x1.5 nuts
Three 70mm 10m x1.5 bolts
Pressure (boost gauge)
Oil lines ( got this kit http://cgi.ebay.com/ebaymotors/ws/e...0213047694&viewitem=&sspagename=STRK:MEWNX:IT )
A turbo master or stuff for building one
Pb blaster
Small block chevy fuel pump block off plate
Electric fuel pump (and a prefilter for it)
The first step for me started about a week before the turbo was set to come in. I sprayed all bolts that I thought I would be removing with pb blaster. The main bolts I was concerned about were the exhaust manifold bolts. For my set up I will only be removing the passenger side manifold. Only one bolt was loose after 2 days of soaking, I stress that patience is the most important part in this step. Do not force the bolts or you will break them and be left with more problems that you need. I used only a 6 inch 3/8 drive ratchet with minimal force for this entire process. By the sixth day with liberal coatings of pb blaster six of the eight bolts were loose and could be removed easily. The other two were still firmly seated, I used a mapp gas torch to heat the portion of the bolt between the manifold and the head. After several repeats of this process all of the bolts were loose and ready for removal.
Next of course is the removal of the exhaust manifold and the exhaust system. Start by removing the exhuast system, you will pretty much need a sawzall or a cutting torch or this could take a while. I left the drivers side manifold and about 6 inches of pipe. If you plan to have a professionally made crossover I would recommend removing the whole system.
I didn't do it in this order but if I would do it again I would do it this way. Remove the mechanical lift pump (this will be much easier to do with out the manifold in the way). I got a shiny chrome fuel pump block off plate for a small block chevy from my local parts store. Note: the top two supplied bolts will work but you will have to reuse your bottom bolts from the lift pump. I used a oil return line from the kit I bought here: http://cgi.ebay.com/ebaymotors/ws/e...0213047694&viewitem=&sspagename=STRK:MEWNX:IT
I drilled a 5/8ths hole in the middle of the block off plate and the included gasket with a drill press and threaded the two sides of a fitting to get this:
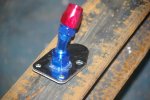
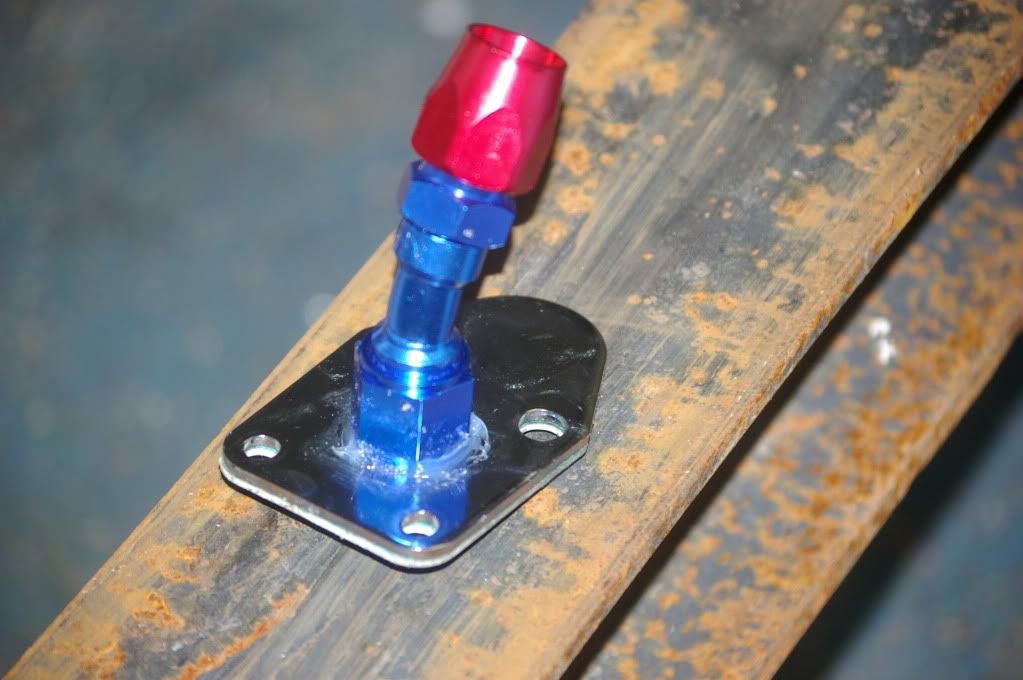
Also install the oil return plate on the turbo (included with the above kit). And the long angled blue arm.
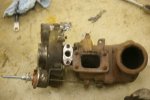
When I removed my exhaust manifold the bolts were in pretty bad shape so I decided to chase the threads on the head. I used a 10Mx1.5 tap to smooth out all of the threads for the new bolts.
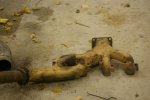
In my case I actually welded a piece to my manifold, again, have it done professionally or do something less jimmy-rigged than mine
.
The next step is to install the manifold using your five 90mm 10m x1.5 studs and three 70mm 10m x1.5 bolts. The short bolts will be used on the first three wholes closest to the radiator and the studs will be used on all the remaining wholes. Before you install carefully bend all glowplug tabs upwards (towards the hood). Also a few tricks: Use some silicone rtv to hold the two gaskets together and in place on the manifold. I also used a little on all of the bolts and studs so they would not slide down when I was trying to install. This job can be simplified with two people, I didn't have that luxury.
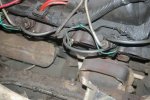
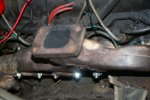
Now before you get carried away installing the turbo, take your time to either make a turbo master or to install one that you have bought. I just welded a piece of all thread to the shaft, used a strong compression spring, and a nylon locking nut. Maybe cost 3 dollars.
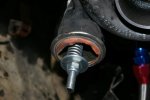
Now it is time to install the turbo. It is pretty much self explanatory, line up the 4 holes and the tighten all nuts to a good snug and even torque.
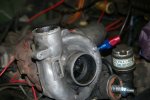
You can go ahead and install your oil return line completely now. Take the tape off the end of the line so it will expand and you can fit it over your compression fitting.

Now is time to install your lower intake manifold, not much to it just time consuming. While it is off go ahead and turn up your fuel pump ¼ turn. I always turn my pumps up through the top, do what ever what you find is easier.
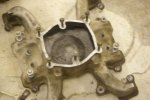
Materials
Borg-Warner GM-x series turbo
Intake manifold
Upper intake manifold
Drivers side exhaust manifold
Two exhuast manifold gaskets for 6.2 diesel motor.
Five 90mm 10m x1.5 studs
Five 10m x1.5 nuts
Three 70mm 10m x1.5 bolts
Pressure (boost gauge)
Oil lines ( got this kit http://cgi.ebay.com/ebaymotors/ws/e...0213047694&viewitem=&sspagename=STRK:MEWNX:IT )
A turbo master or stuff for building one
Pb blaster
Small block chevy fuel pump block off plate
Electric fuel pump (and a prefilter for it)
The first step for me started about a week before the turbo was set to come in. I sprayed all bolts that I thought I would be removing with pb blaster. The main bolts I was concerned about were the exhaust manifold bolts. For my set up I will only be removing the passenger side manifold. Only one bolt was loose after 2 days of soaking, I stress that patience is the most important part in this step. Do not force the bolts or you will break them and be left with more problems that you need. I used only a 6 inch 3/8 drive ratchet with minimal force for this entire process. By the sixth day with liberal coatings of pb blaster six of the eight bolts were loose and could be removed easily. The other two were still firmly seated, I used a mapp gas torch to heat the portion of the bolt between the manifold and the head. After several repeats of this process all of the bolts were loose and ready for removal.
Next of course is the removal of the exhaust manifold and the exhaust system. Start by removing the exhuast system, you will pretty much need a sawzall or a cutting torch or this could take a while. I left the drivers side manifold and about 6 inches of pipe. If you plan to have a professionally made crossover I would recommend removing the whole system.
I didn't do it in this order but if I would do it again I would do it this way. Remove the mechanical lift pump (this will be much easier to do with out the manifold in the way). I got a shiny chrome fuel pump block off plate for a small block chevy from my local parts store. Note: the top two supplied bolts will work but you will have to reuse your bottom bolts from the lift pump. I used a oil return line from the kit I bought here: http://cgi.ebay.com/ebaymotors/ws/e...0213047694&viewitem=&sspagename=STRK:MEWNX:IT
I drilled a 5/8ths hole in the middle of the block off plate and the included gasket with a drill press and threaded the two sides of a fitting to get this:
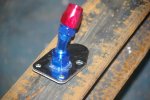
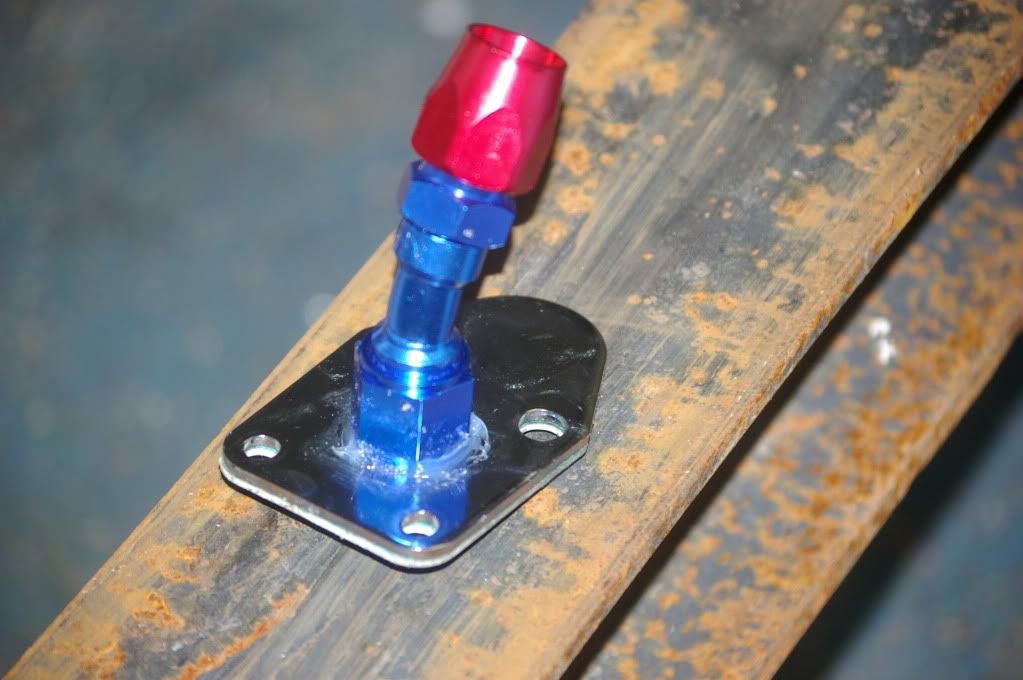
Also install the oil return plate on the turbo (included with the above kit). And the long angled blue arm.
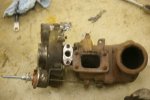
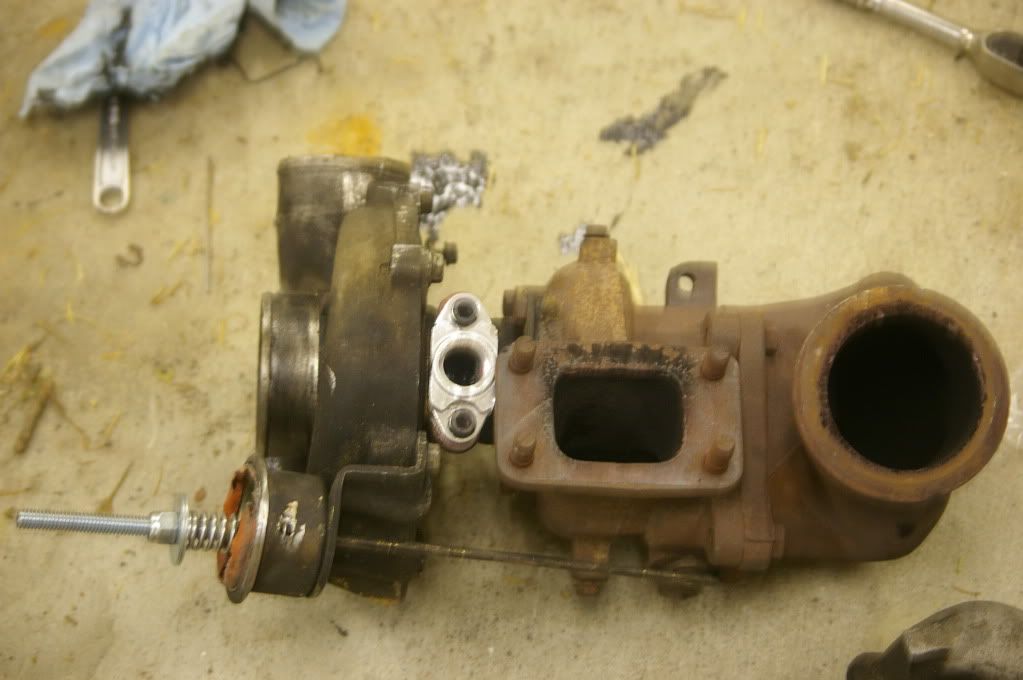
When I removed my exhaust manifold the bolts were in pretty bad shape so I decided to chase the threads on the head. I used a 10Mx1.5 tap to smooth out all of the threads for the new bolts.
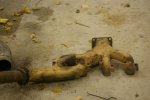
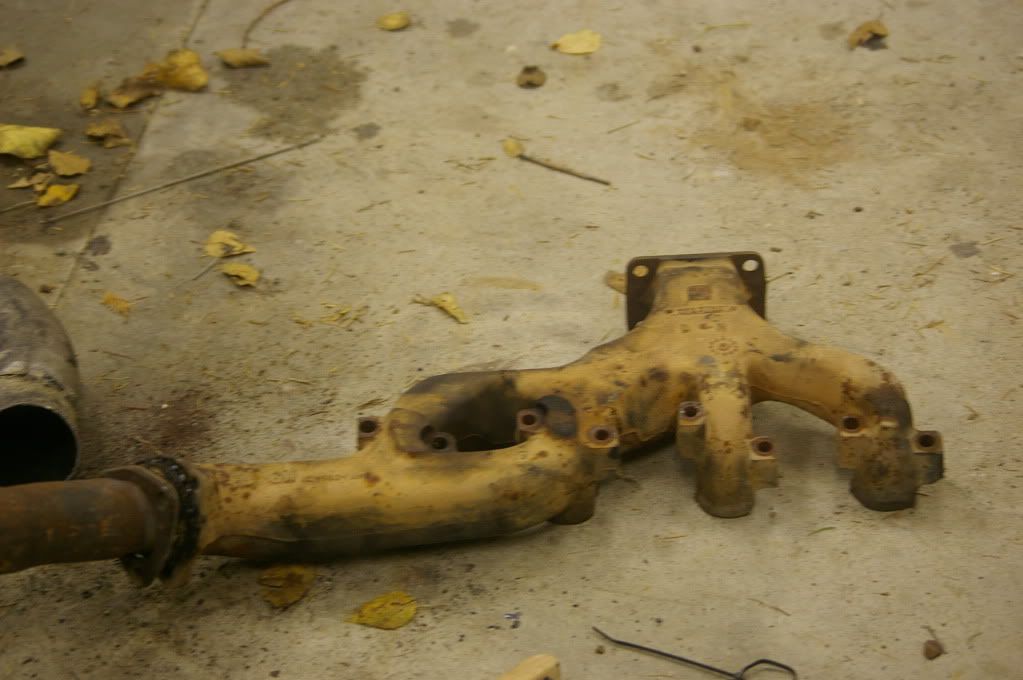
In my case I actually welded a piece to my manifold, again, have it done professionally or do something less jimmy-rigged than mine
The next step is to install the manifold using your five 90mm 10m x1.5 studs and three 70mm 10m x1.5 bolts. The short bolts will be used on the first three wholes closest to the radiator and the studs will be used on all the remaining wholes. Before you install carefully bend all glowplug tabs upwards (towards the hood). Also a few tricks: Use some silicone rtv to hold the two gaskets together and in place on the manifold. I also used a little on all of the bolts and studs so they would not slide down when I was trying to install. This job can be simplified with two people, I didn't have that luxury.
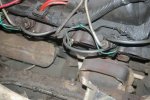
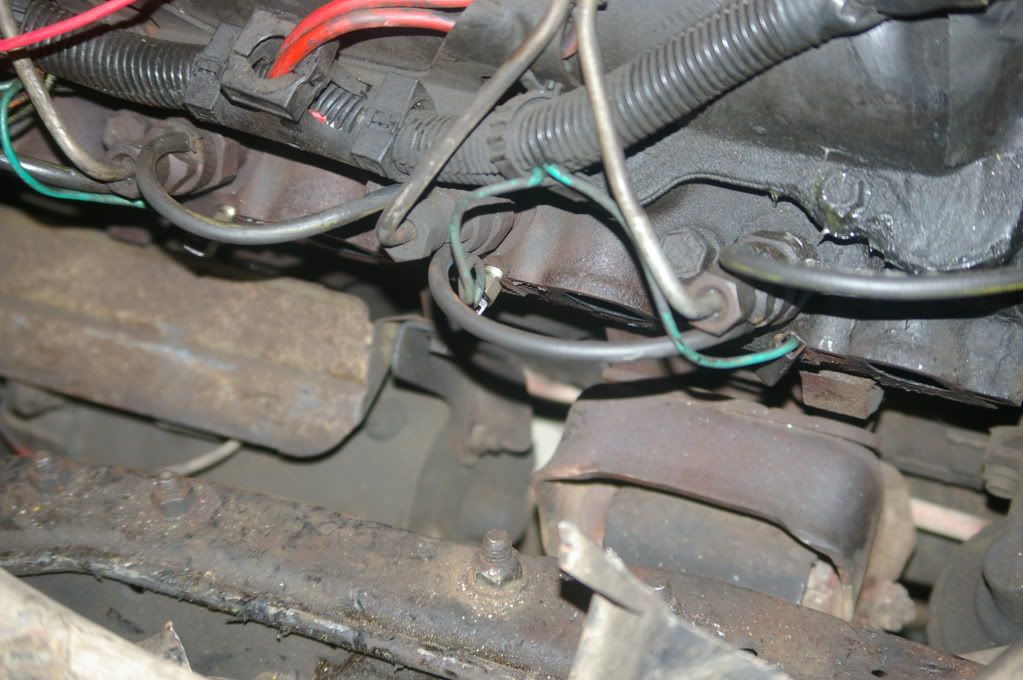
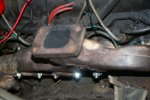
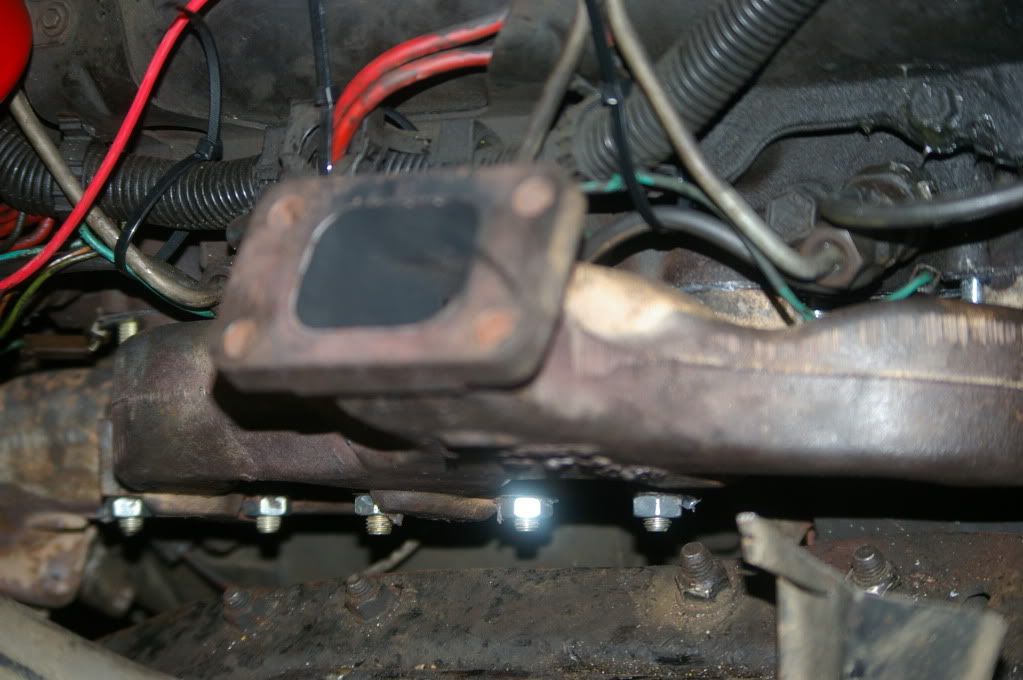
Now before you get carried away installing the turbo, take your time to either make a turbo master or to install one that you have bought. I just welded a piece of all thread to the shaft, used a strong compression spring, and a nylon locking nut. Maybe cost 3 dollars.
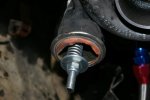
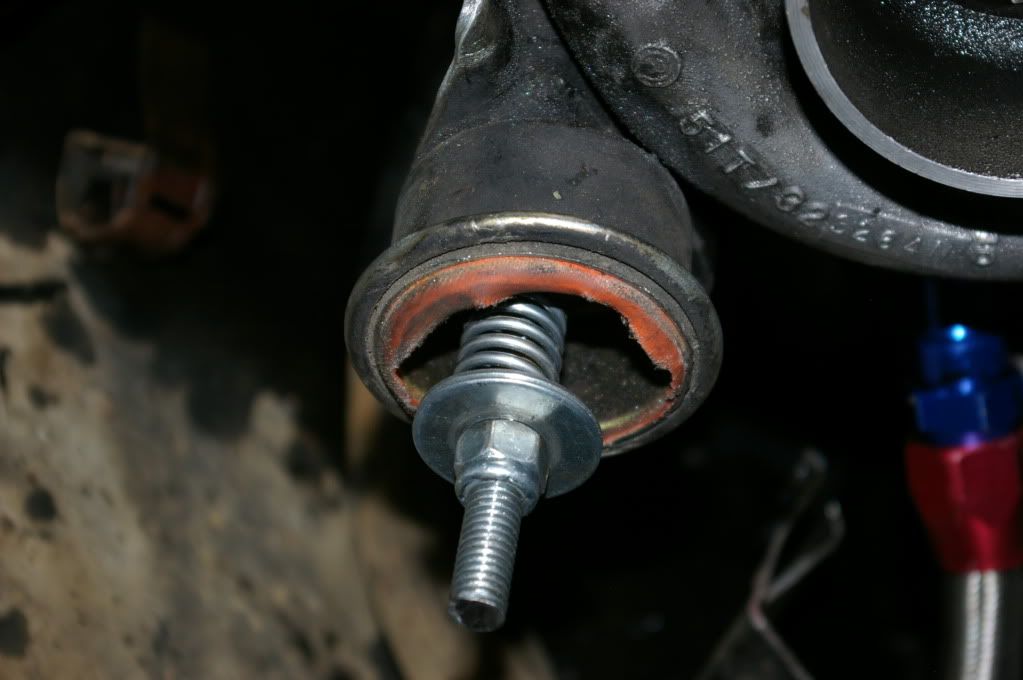
Now it is time to install the turbo. It is pretty much self explanatory, line up the 4 holes and the tighten all nuts to a good snug and even torque.
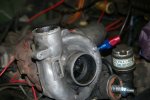
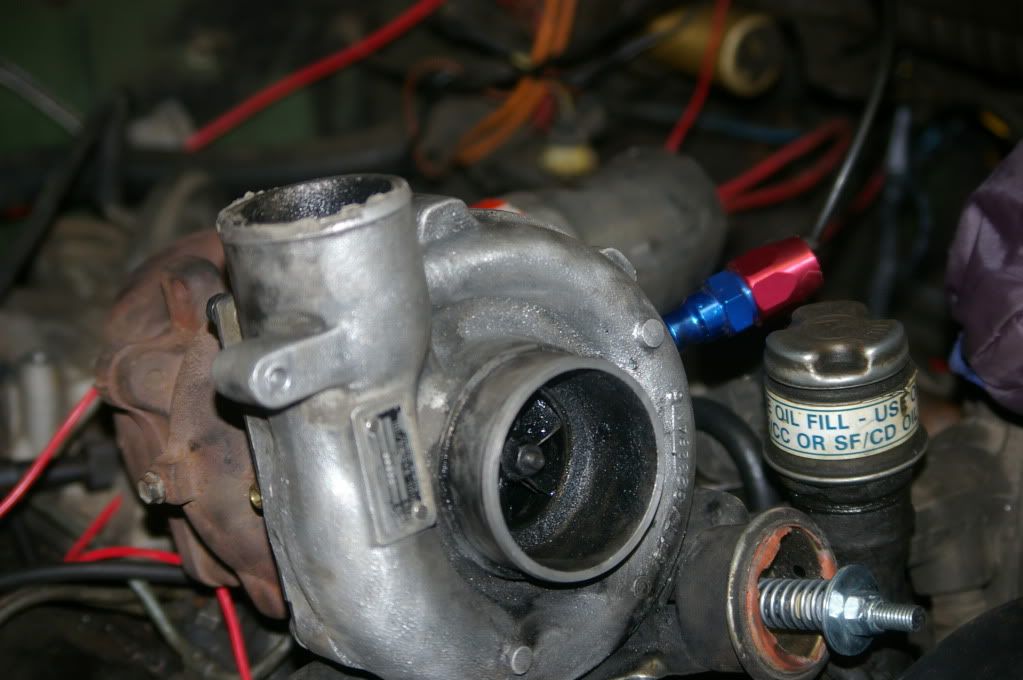
You can go ahead and install your oil return line completely now. Take the tape off the end of the line so it will expand and you can fit it over your compression fitting.

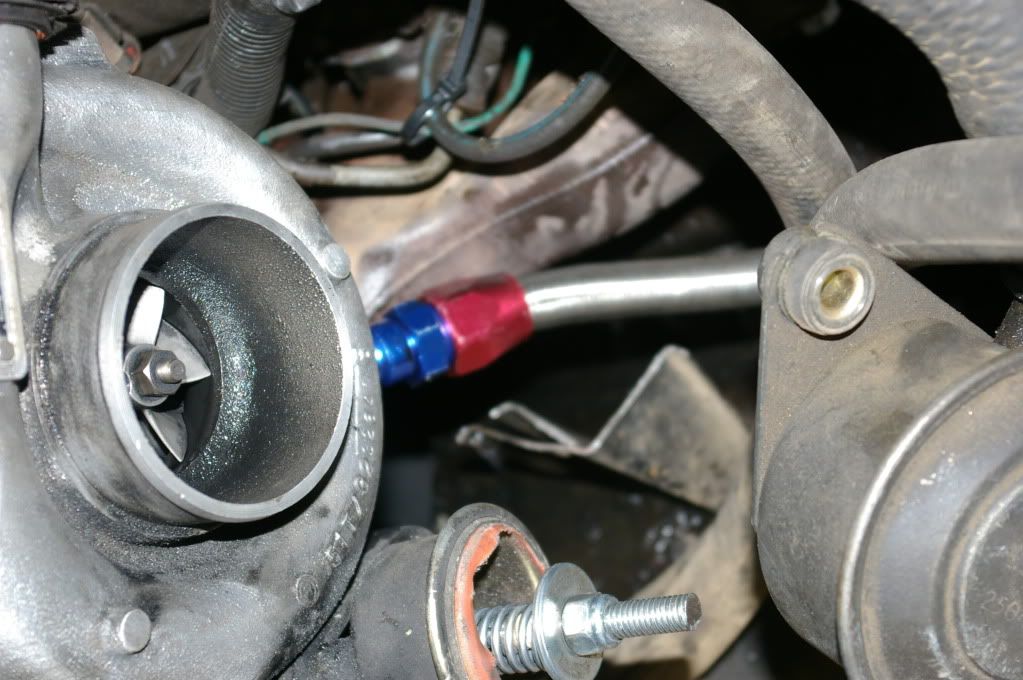
Now is time to install your lower intake manifold, not much to it just time consuming. While it is off go ahead and turn up your fuel pump ¼ turn. I always turn my pumps up through the top, do what ever what you find is easier.
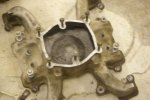
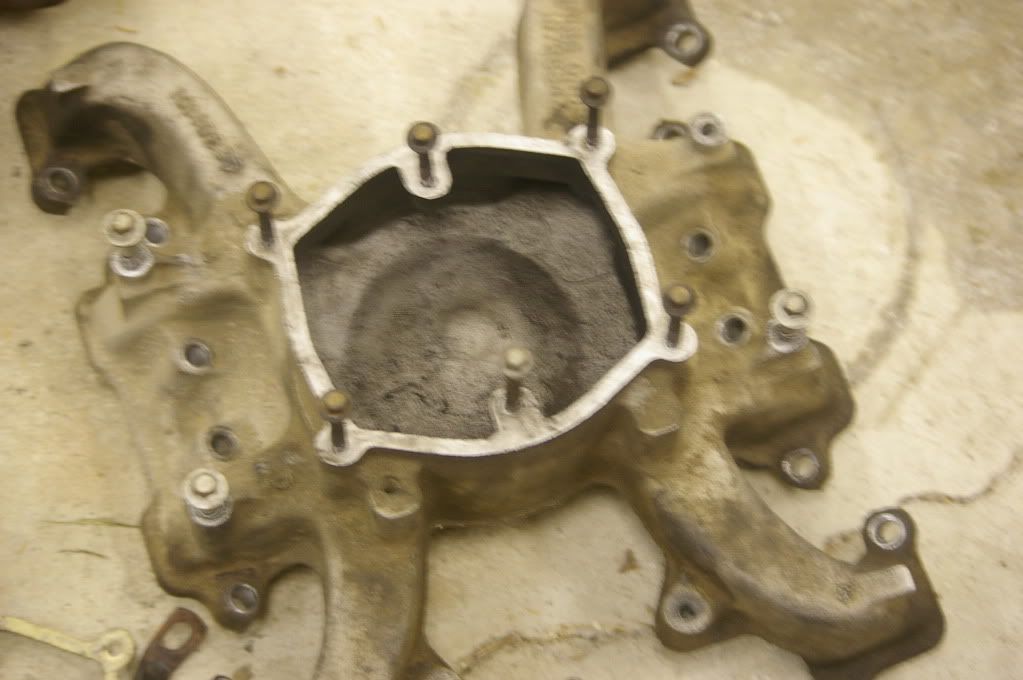
Last edited by a moderator: