- 461
- 78
- 28
- Location
- Beaumont in SoCal
So, as a new owner of an M151A1, I was confused about the hub nuts, how to take them off, how they were designed, etc. In TM 9-2320-218-20, Fig. 2-296 on page 2-179 you can see the lifting eye and locknut, but the copy I have does not offer a clear picture. I had also heard various comments about hitting the locknut with a hammer and drift to loosen or tighten it. Paragraph 2-138 on page 2-182 simply says to remove the nut and lifting eye (no special tools called out). I could not find any instructions in the TM about how tight the lifting eye lock nut is supposed to be. I wasn’t sure if the eye and nut help keep the hub together.
I made a socket out of heavy-wall steel, a large flat washer, and a ¾”-drive socket hub which I cut off of a cheap socket. When I cut the notches on the new socket for the locknut tabs, I made them deeper than the locknut tab thickness and slightly angled so as torque is applied, the socket would be somewhat drawn in toward the hub rather than slipping off.
The first nut I loosened required my ¾”-drive ratchet and a five-foot cheater pipe. The other three could have been loosened with a ½” breaker bar. So the first one would have been pretty tough to beat loose and I know I would have bashed a knuckle or two.
Total time to make the socket was about three hours. The tubing I had on hand was about 3/16” too big, inside diameter, so I had to cut out about ¼” and then close it up with a hydraulic press and weld it solid. If I made another, I would start with a smaller ID and bore it out with a lathe.
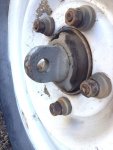
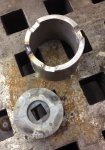
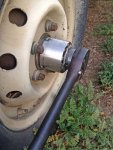
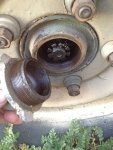
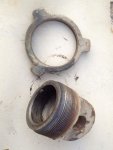
I made a socket out of heavy-wall steel, a large flat washer, and a ¾”-drive socket hub which I cut off of a cheap socket. When I cut the notches on the new socket for the locknut tabs, I made them deeper than the locknut tab thickness and slightly angled so as torque is applied, the socket would be somewhat drawn in toward the hub rather than slipping off.
The first nut I loosened required my ¾”-drive ratchet and a five-foot cheater pipe. The other three could have been loosened with a ½” breaker bar. So the first one would have been pretty tough to beat loose and I know I would have bashed a knuckle or two.
Total time to make the socket was about three hours. The tubing I had on hand was about 3/16” too big, inside diameter, so I had to cut out about ¼” and then close it up with a hydraulic press and weld it solid. If I made another, I would start with a smaller ID and bore it out with a lathe.
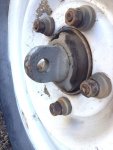
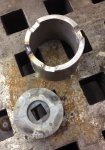
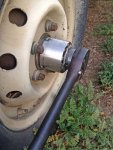
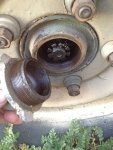
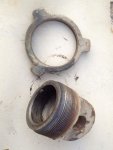