Having the same issue with the main harness rubbing on the back of the 400A alternator on a REV truck. Did you find a good mod to prevent this? If not, I';; just add a wire clamp.
that’s the engine harness, that’s not an issue with 400’s, something else cut that wire or the harness was run incorrectly.
This 400amp issue has been beaten to death On this forum by yours truly, I even fabricated the first conversion to 200amp generator using the
400amp bracket. Since than, I no longer replace the 400 unless it just flat out fails.
There are two types of trucks with the 400amp, one is a factory truck, and one is a truck that had the 400 installed as part of an MWO, I’ve found the trucks that were MWO’d had the issue or trucks that went through a full reset.
The problem was the angle the body harness took when exiting the firewall on the driver footwell, this “angle” as i will call it, can’t be changed once the harness is laid in during production. For MWO trucks, you used the provided split loom and tie wraps on the body harness to prevent chafing of the harness, and I must say, not too successfully, the generator fan shroud and vibration would easily cut through the split loom and the harness wrapping, the wires commonly affected were the front light harness branch and if on the main branch, it would be the TPS “throttle position senor” wires, as they are in the harness on the outside of the bundle, I’ve personally and successfully repaired numerous non-shifting trucks here in the shop. I have also started putting about a 3in piece of edge guard on the cooling fan shroud on the generator.
Anyone who buys a turbo truck can immediately perform a check from underneath, this pic I’ve attached is an offending generator and this truck is experiencing shifting issues that can’t be explained…till now, this scenario plays out monthly.
I don’t see this issue on factory trucks, the harness in most cases is an inch or more separation from contacting the rear cooling shroud.
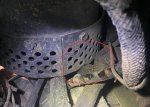