hklvette
New member
- 373
- 7
- 0
- Location
- Christiansburg, VA
So some folks asked me to outline the things I discovered while rebuilding my CTIS and what function each part performs, so here goes…
Preface:
Clean and dry air is essential to the CTIS’ performance. It would be wise to service the Haldex air dryer under the truck before attempting to restore the CTIS function. Also, to inflate requires the controller to see ~120psi before it will activate without error. For reference, my truck is set to cut off between 125 and 130psi. In addition, it is very helpful to have an off-board air supply (like a shop compressor) to supply air to the truck through the front emergency glad-hand to make listening for air leaks much easier.
I) The Wheel Valve
If you have one tire that constantly leaks down, the problem can be here if it’s not the wheel/tire itself or the hose that connects the valve to the wheel. What it is caused by is the diaphragm inside not sealing against the seat (in the center) properly. In the picture below the seat is in the middle of each valve, and the diaphragm is not pictured but sits right on top pressed down by a cup and spring. Of the 13 wheel valves that I disassembled, only four had valve seats in pristine condition. The rest had varying amounts of rust coating the exposed surfaces. They clean off easily with a wire-wheel but stainless pits when it rusts so if they get too rusty cleaning them won’t be enough to restore a good seal. The good news is that they appear to have been made from 5/16-24 stainless steel cap screws and machined into their shape.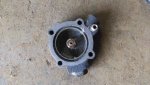
Another issue with the wheel valve is the design of the brass nut and rubber grommet that attaches to the inlet. Out of the 13 wheel valves I have on hand, about half of them have the first 3 threads of the valve body either stripped or corroded off. I believe the reason for this is that the brass nut is not threaded all the way to then end. What I did is used a lathe to cut down the nut so that it was fully threaded inside, and cut down the rubber grommet inside by slightly more. What this allows is the nut to fully engage all of the threads on the housing, reducing the chances of stripping them.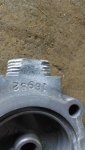
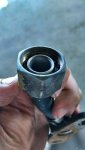
Rebuild kit: Eaton PN 599913
Filter kit (4 per box): Eaton PN 599791
The seats are not in the kit and not available aftermarket per Dana/ Eaton. Recommend consulting a machine shop to have them made from 5/16-24 cap screws.
Preface:
Clean and dry air is essential to the CTIS’ performance. It would be wise to service the Haldex air dryer under the truck before attempting to restore the CTIS function. Also, to inflate requires the controller to see ~120psi before it will activate without error. For reference, my truck is set to cut off between 125 and 130psi. In addition, it is very helpful to have an off-board air supply (like a shop compressor) to supply air to the truck through the front emergency glad-hand to make listening for air leaks much easier.
I) The Wheel Valve
If you have one tire that constantly leaks down, the problem can be here if it’s not the wheel/tire itself or the hose that connects the valve to the wheel. What it is caused by is the diaphragm inside not sealing against the seat (in the center) properly. In the picture below the seat is in the middle of each valve, and the diaphragm is not pictured but sits right on top pressed down by a cup and spring. Of the 13 wheel valves that I disassembled, only four had valve seats in pristine condition. The rest had varying amounts of rust coating the exposed surfaces. They clean off easily with a wire-wheel but stainless pits when it rusts so if they get too rusty cleaning them won’t be enough to restore a good seal. The good news is that they appear to have been made from 5/16-24 stainless steel cap screws and machined into their shape.
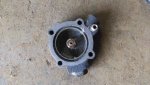
Another issue with the wheel valve is the design of the brass nut and rubber grommet that attaches to the inlet. Out of the 13 wheel valves I have on hand, about half of them have the first 3 threads of the valve body either stripped or corroded off. I believe the reason for this is that the brass nut is not threaded all the way to then end. What I did is used a lathe to cut down the nut so that it was fully threaded inside, and cut down the rubber grommet inside by slightly more. What this allows is the nut to fully engage all of the threads on the housing, reducing the chances of stripping them.
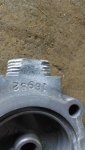
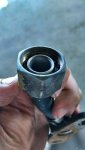
Rebuild kit: Eaton PN 599913
Filter kit (4 per box): Eaton PN 599791
The seats are not in the kit and not available aftermarket per Dana/ Eaton. Recommend consulting a machine shop to have them made from 5/16-24 cap screws.
Last edited: