lino
Member
- 148
- 2
- 18
- Location
- Wake Forest, NC
Hey All,
The perfectionist side of me and the OCD side ganged up on me last night and I couldn't sleep because I was worried I couldn't get the 45 degree -6 AN fitting out of the inlet to the booster pump, and I really need that to be -8 AN so that it matches all the inlet line that I'm putting in.
So I dug into old posts and my heart sank when Clinto mentioned in one that he's never been able to get that one out... Great. I'm doomed.
Well, it was slightly above freezing tonight, instead of slightly below, so I was a little more light-hearted when I got under the truck for my daily "after-the-kids-are-in-bed-wrenching-time".
I started with the feed for the flame heater (which I removed last night). Having read the recommendation to remove the 7/16 fitting and tube first, then use a socket with u-joint + wobble extension, I went to it. It worked well - from above. I started from below, with much less success. So that's out, and a nice hex drive plug in its place.
Then I wanted to remove both the inlet and outlet from the bottom of the booster pump... Gulp.
But, I recalled that I've been removing stuck things out of places you can't reach well or see, or both, for years (err, decades, now I guess). This one, you can see and touch at the same time! Boost of confidence, and away I went.
5 minutes later:
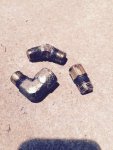
All fittings out of the booster pump.
So tonight I'll be able to sleep.
The fuel fittings, hose, etc should be here tomorrow. As should some airpacks (and rebuild kits), a remote reservoir MC from Peashooter, and a gallon of DOT 5.
I couldn't find a reservoir I liked, so I designed this one, and will be machining it this weekend.
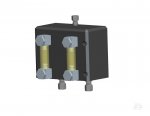
The upper fitting is to vent, but the vent line will have a quick release plug to fit into either the vent manifold (similar to Peashooter's) or into my pressure bleeder. The yellow things hanging off the front in the cad pic are sight tubes, so I won't have to open it to check it. (rated for 150 psi and compatible with DOT 5).
I also bought some wix filter brackets and (oddly), I can't stand the quality of the US made ones, but the Chinese one appears to be pretty good. All WIX brand. The China one will hold the first filter, which will be right by the tank, just as Rustystud did.
So... I also didn't like the way that the two filter brackets have to be serially linked (like the way Rustystud did), so I'll be machining a dual filter bracket shortly too, with all the cross plumbing done internally. I bought the overflow valve too, but I think I might integrate that into the housing as well... More on that after I finish the brakes and fuel lines.
ciao
lino
The perfectionist side of me and the OCD side ganged up on me last night and I couldn't sleep because I was worried I couldn't get the 45 degree -6 AN fitting out of the inlet to the booster pump, and I really need that to be -8 AN so that it matches all the inlet line that I'm putting in.
So I dug into old posts and my heart sank when Clinto mentioned in one that he's never been able to get that one out... Great. I'm doomed.
Well, it was slightly above freezing tonight, instead of slightly below, so I was a little more light-hearted when I got under the truck for my daily "after-the-kids-are-in-bed-wrenching-time".
I started with the feed for the flame heater (which I removed last night). Having read the recommendation to remove the 7/16 fitting and tube first, then use a socket with u-joint + wobble extension, I went to it. It worked well - from above. I started from below, with much less success. So that's out, and a nice hex drive plug in its place.
Then I wanted to remove both the inlet and outlet from the bottom of the booster pump... Gulp.
But, I recalled that I've been removing stuck things out of places you can't reach well or see, or both, for years (err, decades, now I guess). This one, you can see and touch at the same time! Boost of confidence, and away I went.
5 minutes later:
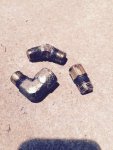
All fittings out of the booster pump.
So tonight I'll be able to sleep.
The fuel fittings, hose, etc should be here tomorrow. As should some airpacks (and rebuild kits), a remote reservoir MC from Peashooter, and a gallon of DOT 5.
I couldn't find a reservoir I liked, so I designed this one, and will be machining it this weekend.
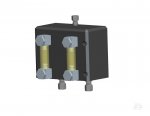
The upper fitting is to vent, but the vent line will have a quick release plug to fit into either the vent manifold (similar to Peashooter's) or into my pressure bleeder. The yellow things hanging off the front in the cad pic are sight tubes, so I won't have to open it to check it. (rated for 150 psi and compatible with DOT 5).
I also bought some wix filter brackets and (oddly), I can't stand the quality of the US made ones, but the Chinese one appears to be pretty good. All WIX brand. The China one will hold the first filter, which will be right by the tank, just as Rustystud did.
So... I also didn't like the way that the two filter brackets have to be serially linked (like the way Rustystud did), so I'll be machining a dual filter bracket shortly too, with all the cross plumbing done internally. I bought the overflow valve too, but I think I might integrate that into the housing as well... More on that after I finish the brakes and fuel lines.
ciao
lino