lino
Member
- 148
- 2
- 18
- Location
- Wake Forest, NC
License plate "Frame"
So, here's a little post on how I mounted the license plate.
I wanted a protected place to put it that wasn't hanging down like an afterthought.
I realize my solution might be blasphemous to some, but so be it... I rather like how it turned out.
The best spot, IMHO, is to the right of center on the rear bed panel, opposite the pocket for the trailer connector.
I wanted the solution to look "factory" (although I grant that no license plate on an MV can look "factory"), so I copied the method used to mount the trailer plug.
First I cut the hole. Non-trivial, it turns out. I didn't measure, but the panel is somewhere between .125 and .188 thick.
I debated between free-hand plasma, stenciled plasma, Mag-drill and holesaw + grinder as methods of removal.
I didn't have a bit large enough on my magdrill for the radius I wanted so that was out.
I taped the outline of the cutout and started with a holesaw (in hand drill) in the corner, and that clearly wasn't going to cut it (literally).
so I used the hole saw to mark the radii, and switched to freehand plasma. Straights were against straightedge, corners-freehand
That worked pretty well, but I had to weld up a few over-runs, hence the little welder in the pic. But all in all, it came out pretty well. In the second pic, you can barely see, but I had to notch the bed frame a little, but it wasn't attached to anything at that point, so structurally, no loss.
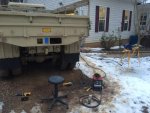
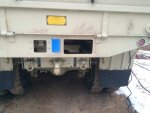
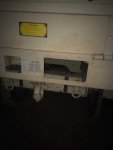
Then on to the bracket. In the keeping of "like the trailer plug method", I wanted a plate with two bends on each side giving an offset of about an inch, with the whole thing a bit bigger than the opening.
I found a suitable piece of 1/8 steel in the scrap pile and got it cut to size.
I have two sheet metal brakes right now. One little one that replaces vise jaws. 8" wide, at that length, max thickness is probably about .030" It couldn't touch the 1/8 plate.
I also have a large one, home brew that fits in a 20 ton press. Should be good to about 3/8'. But that one can't put bends closer than about 3" to each other.
I hate being under-tooled... But bending was out.
So I switched plans to welding and dug out some 1" angle...
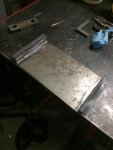
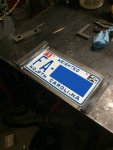
Then for lights, I started with ThoseMilitaryGuys light kit and put it on the plate. Added riv-nuts for the license plate.
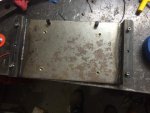
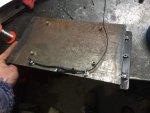
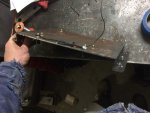
And here is what the plate looks like installed. I still have to replace the SHCS with hex heads to match.
I've also replaced the light kit with a six LED 24v unit from pilotlights.net, that way I don't need the regulator, which I might have already popped.
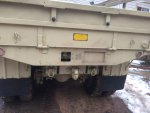
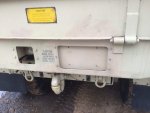
Overall, I'm quite happy with how it turned out.
So, here's a little post on how I mounted the license plate.
I wanted a protected place to put it that wasn't hanging down like an afterthought.
I realize my solution might be blasphemous to some, but so be it... I rather like how it turned out.
The best spot, IMHO, is to the right of center on the rear bed panel, opposite the pocket for the trailer connector.
I wanted the solution to look "factory" (although I grant that no license plate on an MV can look "factory"), so I copied the method used to mount the trailer plug.
First I cut the hole. Non-trivial, it turns out. I didn't measure, but the panel is somewhere between .125 and .188 thick.
I debated between free-hand plasma, stenciled plasma, Mag-drill and holesaw + grinder as methods of removal.
I didn't have a bit large enough on my magdrill for the radius I wanted so that was out.
I taped the outline of the cutout and started with a holesaw (in hand drill) in the corner, and that clearly wasn't going to cut it (literally).
so I used the hole saw to mark the radii, and switched to freehand plasma. Straights were against straightedge, corners-freehand
That worked pretty well, but I had to weld up a few over-runs, hence the little welder in the pic. But all in all, it came out pretty well. In the second pic, you can barely see, but I had to notch the bed frame a little, but it wasn't attached to anything at that point, so structurally, no loss.
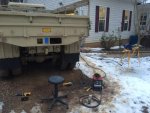
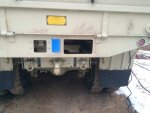
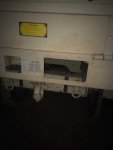
Then on to the bracket. In the keeping of "like the trailer plug method", I wanted a plate with two bends on each side giving an offset of about an inch, with the whole thing a bit bigger than the opening.
I found a suitable piece of 1/8 steel in the scrap pile and got it cut to size.
I have two sheet metal brakes right now. One little one that replaces vise jaws. 8" wide, at that length, max thickness is probably about .030" It couldn't touch the 1/8 plate.
I also have a large one, home brew that fits in a 20 ton press. Should be good to about 3/8'. But that one can't put bends closer than about 3" to each other.
I hate being under-tooled... But bending was out.
So I switched plans to welding and dug out some 1" angle...
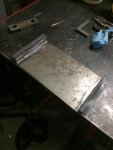
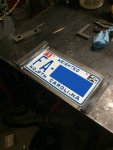
Then for lights, I started with ThoseMilitaryGuys light kit and put it on the plate. Added riv-nuts for the license plate.
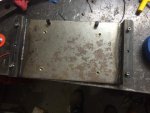
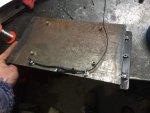
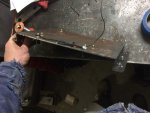
And here is what the plate looks like installed. I still have to replace the SHCS with hex heads to match.
I've also replaced the light kit with a six LED 24v unit from pilotlights.net, that way I don't need the regulator, which I might have already popped.
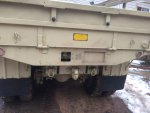
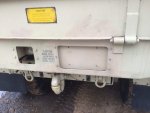
Overall, I'm quite happy with how it turned out.
Last edited: