- 1,962
- 433
- 68
- Location
- Culver City, CA
I took one of my old 20" rims and made a hub/brake drum puller/installer jig that adapts to my floor jack.
I cut the rim in half and removed some of the rim lip as to not interfere with the jack. I drilled a 7/8" hole at the bottom center of the rim half. I removed the jack's lifting plate and attached the jig using a 3/4" bolt, nut and flat washer leaving it a little loose so the jig can rotate and have a little up and down movement.
It worked like a charm. No aching back here!! I just it ran up against the hub/drum, snugged up several lug nuts and pulled the hub/drum straight off. If you set some 2X4's on the ground you can rotate the jack up 90 degrees and remove the hub/drum setting it on the blocks. Then you can go grab the next one.
Installation was just as easy. I used a bottle jack to get the axle at that sweet spot for optimum installation. The hub/drum slipped on the spindle with little coaxing.
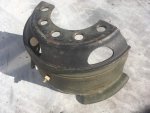
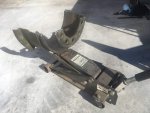
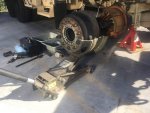
I cut the rim in half and removed some of the rim lip as to not interfere with the jack. I drilled a 7/8" hole at the bottom center of the rim half. I removed the jack's lifting plate and attached the jig using a 3/4" bolt, nut and flat washer leaving it a little loose so the jig can rotate and have a little up and down movement.
It worked like a charm. No aching back here!! I just it ran up against the hub/drum, snugged up several lug nuts and pulled the hub/drum straight off. If you set some 2X4's on the ground you can rotate the jack up 90 degrees and remove the hub/drum setting it on the blocks. Then you can go grab the next one.
Installation was just as easy. I used a bottle jack to get the axle at that sweet spot for optimum installation. The hub/drum slipped on the spindle with little coaxing.
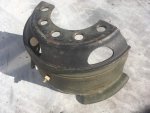
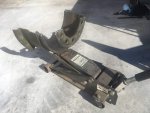
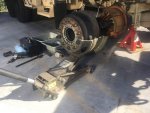