aleigh
Well-known member
- 1,040
- 52
- 48
- Location
- Phoenix, AZ & Seattle, WA
I've mentioned some of this before in different threads but I thought I would summarize it here. There are a lot of great threads about the FMTV hydraulic system, but these are some less common tidbits.
-= Corrosion =-
My manifold and pump were badly corroded; the valves so bad that eventually they failed. I don't think I have seen a rebuild of a used SPX power pack yet where the pump was not corroded. It seems counter-intuitive that things immersed in oil rust, but this is very much the case. Unlike a hydraulic brake or clutch system in a car, the FMTV circuit is exposed to air through the reservoir vent. When the oil level drops or pressure changes, air will be drawn into the reservoir. Humidity in that air well condense on the walls of the tank and eventually into the fluid, where it will circulate.
The SPX power pack has a desiccant filter on it which is designed to dry the air entering the tank to prevent this problem. The thing about desiccant filters is they have a finite service life and once they are used up, wet air will be drawn in. Replace on a schedule and ensure you are using fluid with modern anti-corrosive properties.
-= Hose Length =-
If you encounter any kind of problem with the hydraulic system, odds are you are going to have to get into the manifold. Although the spool valves and pneumatic switches can be removed from the front and the filters from the top, the check valves come out the side. This, and anything to do with the hoses, basically requires removing the manifold from the truck.
The people built the truck gave the hoses exactly the right length and not a hair more. Consequently, to remove the hoses you have to get a wrench down into the gap from the side (above the fuel tank) or top. There is so little room to work here, the cab lift hoses are on elbows. It's terrible. It's just beyond terrible. And if you have to do any kind of trial and error testing you are going to be miserable.
The solution for me was to have hose extensions made. They are JIC fittings and the local hydraulic hose place took one look at it, and 20 minutes later I had 10 18" hoses and was $200 lighter. This is the best money I have ever spent on the truck. This gives enough slack that the manifold can be removed and sat on a ladder or whatever else is handy. To extend the air lines I went and got more DOT tubing and some female to female connectors from NAPA. I also replaced the connectors on the manifold with the QD style.
If you take the truck off road or anything like that where there is a risk you are going to have to work on things or patch things up, just do this now before you wish you had. You were warned...
-= Return Lines Are Common =-
This was my biggest AHA.
When something goes wrong with the system, such as a leak in a hose, the system can act surprisingly. For example, a hose cut on the tire crane will effect lifting the cab - sometimes. This was a real puzzler to me until I reviewed the schematics. It drove me crazy, why would it leak at one point and then not another? When working on the system it is important to understand that the return lines across all spool valves are tied together, plus the return lines (the T lines) for the pumps, and there are no check valves for the work circuits (suspension, tire, cab) in the manifold itself. There are in the cylinders depending on the circuit, but not in the manifold. Therefore the hoses are unprotected.
An example: If you remove the tire extend hose, set the spool valve to tire retract (tying extend to the return), and then seemingly unrelated try to lift the cab, you will spray fluid everywhere. If you set the tire valve to extend, nothing will come out. Personally I wish they had put one-way valves on the return lines (other than the T returns). The reason you might care about this is when you have a cable or fitting fail and you want the system to work without peeing itself. If you remember this though you can set the spool valve up right for the broken circuit to isolate the line. If you break both lines in one work circuit (like say you disconnect a ram for repairs) you are out of luck.
This also means that you can't just hook up one circuit and one pump. You have to hook up, at minimum, both pumps and 3 work circuit return lines and then set the spools properly.
Normally we think of the return line as being low pressure (after all it is free to flow and we are pumping into the high side). However resistance to the moving parts (like the tire hanging on the crane) will pressurize the return side which must hold fast to prevent the ram from dropping the load. In other words BOTH sides must hold good pressure.
Where this becomes a problem is when something on the return side wants to leak. On my truck, my hand pump eventually started leaking, and would spray fluid on the return side when load was applied to a ram. This was difficult to deal with in the field because unlike the other circuits there is no way to isolate the hand pump. Likewise a pressure failure in the power pack is going to have a similar result.
Consequently I have started carrying around a ziploc of JIC plugs. These are basically plugs with a flange and o-ring. Depending on your manifold part # you may have one already installed in the "suspension normal" plug. The plugs allow me to isolate failed lines or pumps by removing the manifold (now "easy" because I have slack, removing the hose and fitting, and plugging the circuits). If you carry enough you can remove everything except a pump circuit and the cab lift, for example.
-= Puffing is probably but maybe not bad =-
If your pump into an impossible load the power pack will vent fluid. This can happen during certain failure scenarios (like stuck check valves, etc). This is commonly taken as a sign that the seals are bad and the power pack must be rebuilt, but not necessarily. If your pack is not puffing when the hydraulics are otherwise operating normally (like when you lift a tire), it is fine. I suppose either accidentally or by design this is its version of high-pressure bypass. The manual pump has a relief valve on the high pressure side which ties to the low side. Which brings us to
-= The hand pump has a relief valve on the high pressure side which ties to the low side =-
What this means is that if the valve fails, when you pump on the high side it will equally (or partially?) put pressure into the return side. You thought it vented to air, right? I sure did. I guess despite a cat engine and a SPX power pack they decided this was their red line and it was not going to leak.
A failed bypass is not necessarily obvious but it will be obvious that the rams are not moving or generally fighting against themselves. And of course there is no way to isolate the hand pump at the side of the road unless you have taken the earlier advice.
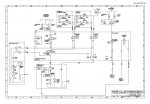
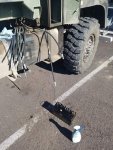
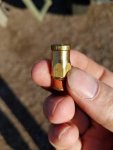
-= Corrosion =-
My manifold and pump were badly corroded; the valves so bad that eventually they failed. I don't think I have seen a rebuild of a used SPX power pack yet where the pump was not corroded. It seems counter-intuitive that things immersed in oil rust, but this is very much the case. Unlike a hydraulic brake or clutch system in a car, the FMTV circuit is exposed to air through the reservoir vent. When the oil level drops or pressure changes, air will be drawn into the reservoir. Humidity in that air well condense on the walls of the tank and eventually into the fluid, where it will circulate.
The SPX power pack has a desiccant filter on it which is designed to dry the air entering the tank to prevent this problem. The thing about desiccant filters is they have a finite service life and once they are used up, wet air will be drawn in. Replace on a schedule and ensure you are using fluid with modern anti-corrosive properties.
-= Hose Length =-
If you encounter any kind of problem with the hydraulic system, odds are you are going to have to get into the manifold. Although the spool valves and pneumatic switches can be removed from the front and the filters from the top, the check valves come out the side. This, and anything to do with the hoses, basically requires removing the manifold from the truck.
The people built the truck gave the hoses exactly the right length and not a hair more. Consequently, to remove the hoses you have to get a wrench down into the gap from the side (above the fuel tank) or top. There is so little room to work here, the cab lift hoses are on elbows. It's terrible. It's just beyond terrible. And if you have to do any kind of trial and error testing you are going to be miserable.
The solution for me was to have hose extensions made. They are JIC fittings and the local hydraulic hose place took one look at it, and 20 minutes later I had 10 18" hoses and was $200 lighter. This is the best money I have ever spent on the truck. This gives enough slack that the manifold can be removed and sat on a ladder or whatever else is handy. To extend the air lines I went and got more DOT tubing and some female to female connectors from NAPA. I also replaced the connectors on the manifold with the QD style.
If you take the truck off road or anything like that where there is a risk you are going to have to work on things or patch things up, just do this now before you wish you had. You were warned...
-= Return Lines Are Common =-
This was my biggest AHA.
When something goes wrong with the system, such as a leak in a hose, the system can act surprisingly. For example, a hose cut on the tire crane will effect lifting the cab - sometimes. This was a real puzzler to me until I reviewed the schematics. It drove me crazy, why would it leak at one point and then not another? When working on the system it is important to understand that the return lines across all spool valves are tied together, plus the return lines (the T lines) for the pumps, and there are no check valves for the work circuits (suspension, tire, cab) in the manifold itself. There are in the cylinders depending on the circuit, but not in the manifold. Therefore the hoses are unprotected.
An example: If you remove the tire extend hose, set the spool valve to tire retract (tying extend to the return), and then seemingly unrelated try to lift the cab, you will spray fluid everywhere. If you set the tire valve to extend, nothing will come out. Personally I wish they had put one-way valves on the return lines (other than the T returns). The reason you might care about this is when you have a cable or fitting fail and you want the system to work without peeing itself. If you remember this though you can set the spool valve up right for the broken circuit to isolate the line. If you break both lines in one work circuit (like say you disconnect a ram for repairs) you are out of luck.
This also means that you can't just hook up one circuit and one pump. You have to hook up, at minimum, both pumps and 3 work circuit return lines and then set the spools properly.
Normally we think of the return line as being low pressure (after all it is free to flow and we are pumping into the high side). However resistance to the moving parts (like the tire hanging on the crane) will pressurize the return side which must hold fast to prevent the ram from dropping the load. In other words BOTH sides must hold good pressure.
Where this becomes a problem is when something on the return side wants to leak. On my truck, my hand pump eventually started leaking, and would spray fluid on the return side when load was applied to a ram. This was difficult to deal with in the field because unlike the other circuits there is no way to isolate the hand pump. Likewise a pressure failure in the power pack is going to have a similar result.
Consequently I have started carrying around a ziploc of JIC plugs. These are basically plugs with a flange and o-ring. Depending on your manifold part # you may have one already installed in the "suspension normal" plug. The plugs allow me to isolate failed lines or pumps by removing the manifold (now "easy" because I have slack, removing the hose and fitting, and plugging the circuits). If you carry enough you can remove everything except a pump circuit and the cab lift, for example.
-= Puffing is probably but maybe not bad =-
If your pump into an impossible load the power pack will vent fluid. This can happen during certain failure scenarios (like stuck check valves, etc). This is commonly taken as a sign that the seals are bad and the power pack must be rebuilt, but not necessarily. If your pack is not puffing when the hydraulics are otherwise operating normally (like when you lift a tire), it is fine. I suppose either accidentally or by design this is its version of high-pressure bypass. The manual pump has a relief valve on the high pressure side which ties to the low side. Which brings us to
-= The hand pump has a relief valve on the high pressure side which ties to the low side =-
What this means is that if the valve fails, when you pump on the high side it will equally (or partially?) put pressure into the return side. You thought it vented to air, right? I sure did. I guess despite a cat engine and a SPX power pack they decided this was their red line and it was not going to leak.
A failed bypass is not necessarily obvious but it will be obvious that the rams are not moving or generally fighting against themselves. And of course there is no way to isolate the hand pump at the side of the road unless you have taken the earlier advice.
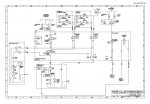
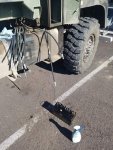
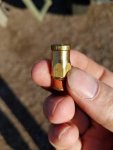