- 2,479
- 25
- 38
- Location
- Houston Texas
I started getting tired of the leaks and replacing high dollar parts to keep the fan clutch working. So while looking at some civi H1 stuff on the web I saw a 93 model with v belts and a thermo clutch. I searched for the pulley and parts and found they were discontinued. I decided to come up with something on my own. I picked up a extra water pump pulley from the auction site to use for my mods.
From what I read the H1 has a problem with the hood giving the venturi effect while moving. So air is not being forced through the rad very much. I could see this because My unloaded 2 man 998 will engage the clutch every 2miles or so. Even on a cool day at 40MPH.
So with the stock fan not turning much the engine constantly goes through a heating and cooling cycle. When the fan comes on the temp drops. When off it heats up until the fan comes on and starts all over again.
Reading the Hayden site the thermo clutch will turn 30% of WP speed when not hot. So if that the case then It should pull more air when driving therefore allowing the engine to stay a constant temp. I have this fan and clutch on my M1028A1 and it moves enough air when cold to blow the grass under the truck.
I chucked up my auction site pulley, took some mesurements using a spare 6.2 I have on a stand and machined the pulley to make the thermo clutch fit. When the rain stops I'll put it on the truck and see how well it works.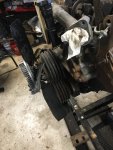
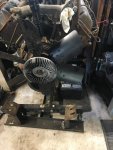
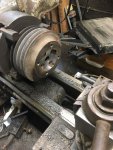
From what I read the H1 has a problem with the hood giving the venturi effect while moving. So air is not being forced through the rad very much. I could see this because My unloaded 2 man 998 will engage the clutch every 2miles or so. Even on a cool day at 40MPH.
So with the stock fan not turning much the engine constantly goes through a heating and cooling cycle. When the fan comes on the temp drops. When off it heats up until the fan comes on and starts all over again.
Reading the Hayden site the thermo clutch will turn 30% of WP speed when not hot. So if that the case then It should pull more air when driving therefore allowing the engine to stay a constant temp. I have this fan and clutch on my M1028A1 and it moves enough air when cold to blow the grass under the truck.
I chucked up my auction site pulley, took some mesurements using a spare 6.2 I have on a stand and machined the pulley to make the thermo clutch fit. When the rain stops I'll put it on the truck and see how well it works.
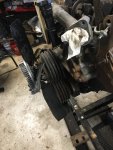
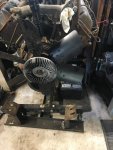
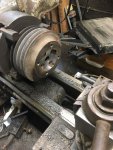