- 849
- 1,740
- 93
- Location
- N. Central Idaho
I heard a rattling sound last drive and discovered a ujoint on the propeller shaft connecting two real diffs was gone. Surprised I made it home. Pulled the shaft and pounded out both of the ujoints. (Tap my arse!) They were snap ring type. Decided when I get my new parts and build it up I will take to have it balanced while it's out.
Checked the next propeller shaft, transfer to forward rear axle, and ujoints were sloppy but not as bad. Pulled it to replace and have balanced.
The second shaft is the bearing cap type. Pulled the bolts and keepers and broke the cap flange off trying to pry one out. Per the TM this happens, just go to the other side and pull the bearing cap then pound the other one out. It broke off too. Caps are stuck bad. Drilled hole in one, slid a small rod through the ujoint to try and drive off the other broken cap. No joy
Need some advice before I get too crazy. I have all of them soaking in kroil but need a better plan.
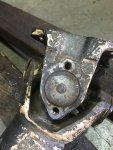
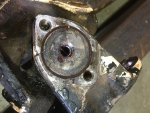
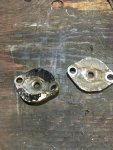
Checked the next propeller shaft, transfer to forward rear axle, and ujoints were sloppy but not as bad. Pulled it to replace and have balanced.
The second shaft is the bearing cap type. Pulled the bolts and keepers and broke the cap flange off trying to pry one out. Per the TM this happens, just go to the other side and pull the bearing cap then pound the other one out. It broke off too. Caps are stuck bad. Drilled hole in one, slid a small rod through the ujoint to try and drive off the other broken cap. No joy
Need some advice before I get too crazy. I have all of them soaking in kroil but need a better plan.
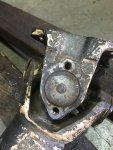
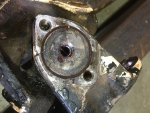
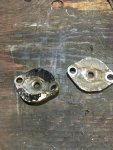