Replace the rotor bearing while you are at it and remove all desert sand in the bottom of the genhead. I actually posted a thread about replacing that without removing the engine but if you area already doing that then should be a lot less cursing in your future.
https://www.steelsoldiers.com/showt...ear-main-seal-replaceable-without-pulling-top
I dont recall part number because its on my notepad, which ill update that post once I find the time to polish it.
I am having trouble finding a replacement rotor bearing. This should be one of the easiest finds though. I came across a freeze plug set (expansion plugs) for the LPW and they wanted $55 for the set. That is a large pill to swallow considering what they are.
I am learning that if you want parts, do not go the Onan route. If it says Onan, the price is jacked beyond belief. For three metering shims (not even enough for one metering pump - your would need about 3+ kits) they want $16.
I find that if I use the Lister Petter stock/parts numbers, I can find more of the parts at substantially less of a cost. I see things that sell for $300 branded Onan and the same item sell for $140 branded Lister Petter.
Anyways, some more work done today. I made a decision, because I have a very bad back from an injury suffered some 30 years ago, I have decided to get something to help me lift heavy items. So today, I went out and bought a Titan gantry crane rated for 2000lbs and the trolley, and then purchased an electric winch also rated for 2000lbs. I have lots of heavy equipment that I move around a lot due to space limitations (mini mill, mini lathe, Delta 10" Table Saw, Delta shop drill press, metal band cutting saw, wood band cutting saw, blah blah..... These are things that have taken me more than a lifetime to collect and I am getting too old to man handle these things. So today I bit the bullet and got the crane and it will work fine for moving these types of gen sets around for work and other things. This really has nothing to do with the genset except is was the final straw and my wife is just going to have to understand that. But she will because she knows how much I can hurt after playing around for just a short time.
So I did some more disassembly of the housing today. Took the bearings to a friend that has owned a machine shop until recently when he retired from work, and he thinks the rod bearings are showing damage due to wear but the what caused the wear is up for debate. Based on the bearings and descriptions and pictures of the crank shaft, he thinks that there may have been oil contamination due to the scarring on the faces of the bearings He also said that given the places of increased wear, it was right at the oil feed points so there was the most contamination at those points on the bearings. He also said that they are definitely not 15 hour bearings but more like the 200 hour bearings with some slight contaminated oil. And of course due to that, it was just another reason to completely burn the house down to ashes - sort to speak - and tear the genset down completely.
I am changing my opinion of how the entire transactions was handled and to find these things out has got me quite angry about what I got from what I was told I was going to get. So we talked/texted about some other items as well.
Got the fuel stop solenoid in the mail today. I do not know just how much of the cabinet I have to take apart to get the generator and motor out as one piece, or to take the generator off of the back of the engine while the engine is still in the generator housing and once disconnected, remove just the motor and leave the generator in the cabinet, much like Demoh did when he changed the seal on the back of his genset without having to remove it from the cabinet.
Some better shorts of the bearings. Had to wait for just the right time of day at the right angle to get these pictures to come out so well, especially when you blow the up.
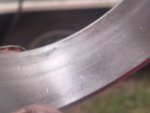
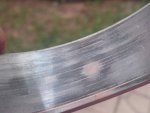
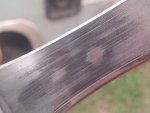
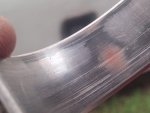
More parts. We have seen the roller lifters for the fuel metering pumps. They are marked to ensure they go back into the right holes. Also the backside of the governor weights that are bolted to the camshaft gear face. The fuel rack or the lever that engages the valves on the bottom of the fuel metering pumps and either turns the fuel on or off. Whether this is immediate and at a precise location on the swing, or it is a long term opening and closing like a water faucet, is not known to me and I can not test this as I do not have the equipment to generate the 3000 to 3500 psi needed to check the fuel pump or the injectors for that matter. I was able to get the fuel rack out of the compartment without taking the front of the compartment off. I did however have to remove the radiator to do it. You can just pull it out and gently nudge it this was and that way being very very very very very careful not to even put the slightest pressure on any part of this rack. About half way through the 1 and 2 (from the back of the engine) fuel metering tabs (for lack of another name) you have to get the entire rack and governor mount rotated 180 degrees (upside down) and take it out. It took me awhile to find the sweet spot and it is a very small sweet spot, but it can be done. And the oil pickup tube.
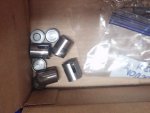
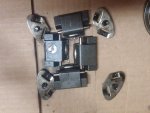
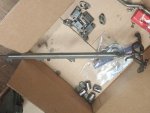
Resolution as to what happened to some of the foam quieting material at the back (control panel) right side. Appears either a chipmunk (to small for a squirrel) or more probably a field mouse made a home.
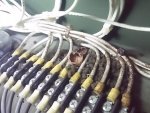
Panel removal. Anybody can tell me what panels I have to remove or do I have to remove all of them for ease.
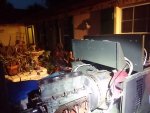
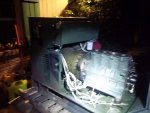