- 1,962
- 433
- 68
- Location
- Culver City, CA
There was nothing wrong with the originals. It was my OCD again
. And, my push to make my truck safer for the civilian road. I recently replaced all the torque rods ends, again, no my M818. I replaced them with the "high-speed" heavy duty torque rod ends that are available through Erik's. These ends will fit all M39, M809, M939 and M939/A1/A2-series 5-ton trucks to include bridge trucks within those series with longer rear wheel centers.
http://www.eriksmilitarysurplus.com/torodendfor51.html
Again, my expenditures and experiences are your gain.
Each one includes the ball joint, castle nut, cotter pin, rubber dust shield and are pre-greased. There is no rubber to rot or tear away from the metal parts. It is a true ball joint with a zerk fitting so the may be periodically greased during vehicle maintenance. The rubber dust shield will help retain excess grease around the inner side of the ball joint. They are quite heavy, nearly 12 lbs. each, and have a very solid outer body. Once pressed into the torque rod, the rod is considerably heavier. The 1/4" lip on the outer edge allow the the torque rod to only press on in one direction. This lip will keep the torque rod from slipping to the outside if there is a catastrophic event. I replaced the cotter pins with the equivalent size in stainless.
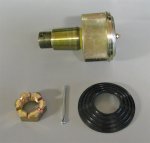
I bought a 4" dia, 1/4" wall, piece of steel tubing cut to 5" long for a pressing arbor. I chose the length in order to also use it to remove these joints as well as install. I had a channel machined at one end 1/8" in and 3/16" down to accommodate the ridge that encircles the face of the joint. The channel locks the arbor in place during pressing. I also bought a 1" thick X 4" dia. slug to span the gap of the tube. These two arbors will also work to press out the OEM ends.
Killed two birds with...two pieces...of...er, steel??
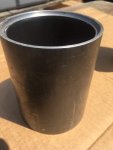
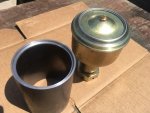
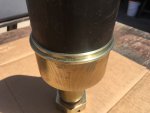
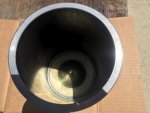
To save on extra costs, I picked up a 20 ton shop press. What have I done without this thing?? No running around town to the shop to do jobs like this, I love it!
Pressing was fairly easy. I used plenty of anti-seize applied inside the torque rod eyes. They start off very smooth then tighten up as they go down. Make sure you start pressing at the chamfered/beveled end of the torque rod. There is a very slight taper on the ball joint and torque rod eye and pressing from that direction will match them up. About 2/3 the way in, they will start to pop every second pump of the jack handle. Press the 1/4" lip on the ball joint to the torque end and they are done.
New ball joints pressed into the torque rods. I found the best way to install the rubber dust shield is to push them down the tapered seat until the outer edge of the shield touches the torque rod eye. If you push the center all the way down to where the tapered seat goes into the ball joint, the outer edge likes to flip up. The shields will not make a good "seal" and allow more grease to drip out. Make sure they are installed prior to seating and tightening the ball joint on the truck. The tapered seats will misalign during handling. I used a rubber hammer to manipulate them to where I needed them by tapping around on them.
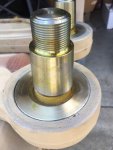
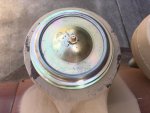
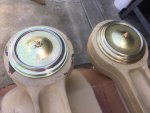
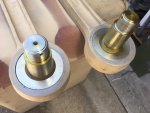
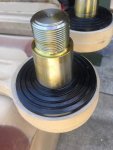
Assembly to the truck is the same as the standard torque rods. They are actually much easier to manipulate into the brackets due to the more flexible nature of them. The axle brackets can been pre-installed due to this. However, the top inner nuts on the trunnion bracket are still a PITA. I just disassembled the leaf spring and rolled it over to gain free access to the nuts. Do the top rods first getting the hard part out of the way. Tighten all castle nuts with hand tools, but never use an impact wrench. The force of the impact wrench will bind up the tapered seats and you'll never get them back out later on.
I regreased the ball joints with some Lucas Heavy Duty green grease. I have an air operated gun and it only takes about a 2 second shot to fill them. I plan to change the two upper axle joint zerk fittings to 90º. Due to clearance issues, It will make greasing those two joints easier than with the straight fittings.
This is the final product. I tested the articulation on a steep driveway at the storage yard and all appears to be OK. An extended road test is still waiting to be done.
I may paint the faces of the two ends visible on either side between the rear tires. The yellowy finish is kind of bothering me.
Anyway, another upgrade job I am glad I tackled.

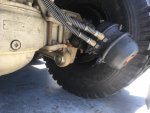
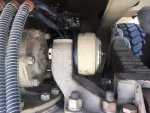
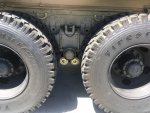
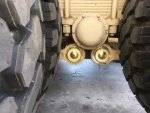

http://www.eriksmilitarysurplus.com/torodendfor51.html
Again, my expenditures and experiences are your gain.
Each one includes the ball joint, castle nut, cotter pin, rubber dust shield and are pre-greased. There is no rubber to rot or tear away from the metal parts. It is a true ball joint with a zerk fitting so the may be periodically greased during vehicle maintenance. The rubber dust shield will help retain excess grease around the inner side of the ball joint. They are quite heavy, nearly 12 lbs. each, and have a very solid outer body. Once pressed into the torque rod, the rod is considerably heavier. The 1/4" lip on the outer edge allow the the torque rod to only press on in one direction. This lip will keep the torque rod from slipping to the outside if there is a catastrophic event. I replaced the cotter pins with the equivalent size in stainless.
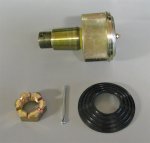
I bought a 4" dia, 1/4" wall, piece of steel tubing cut to 5" long for a pressing arbor. I chose the length in order to also use it to remove these joints as well as install. I had a channel machined at one end 1/8" in and 3/16" down to accommodate the ridge that encircles the face of the joint. The channel locks the arbor in place during pressing. I also bought a 1" thick X 4" dia. slug to span the gap of the tube. These two arbors will also work to press out the OEM ends.
Killed two birds with...two pieces...of...er, steel??


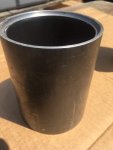
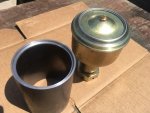
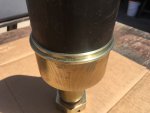
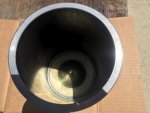
To save on extra costs, I picked up a 20 ton shop press. What have I done without this thing?? No running around town to the shop to do jobs like this, I love it!
Pressing was fairly easy. I used plenty of anti-seize applied inside the torque rod eyes. They start off very smooth then tighten up as they go down. Make sure you start pressing at the chamfered/beveled end of the torque rod. There is a very slight taper on the ball joint and torque rod eye and pressing from that direction will match them up. About 2/3 the way in, they will start to pop every second pump of the jack handle. Press the 1/4" lip on the ball joint to the torque end and they are done.
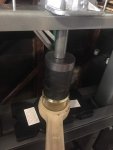
New ball joints pressed into the torque rods. I found the best way to install the rubber dust shield is to push them down the tapered seat until the outer edge of the shield touches the torque rod eye. If you push the center all the way down to where the tapered seat goes into the ball joint, the outer edge likes to flip up. The shields will not make a good "seal" and allow more grease to drip out. Make sure they are installed prior to seating and tightening the ball joint on the truck. The tapered seats will misalign during handling. I used a rubber hammer to manipulate them to where I needed them by tapping around on them.
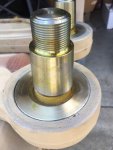
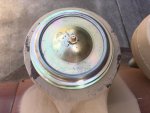
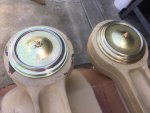
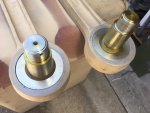
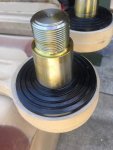
Assembly to the truck is the same as the standard torque rods. They are actually much easier to manipulate into the brackets due to the more flexible nature of them. The axle brackets can been pre-installed due to this. However, the top inner nuts on the trunnion bracket are still a PITA. I just disassembled the leaf spring and rolled it over to gain free access to the nuts. Do the top rods first getting the hard part out of the way. Tighten all castle nuts with hand tools, but never use an impact wrench. The force of the impact wrench will bind up the tapered seats and you'll never get them back out later on.
I regreased the ball joints with some Lucas Heavy Duty green grease. I have an air operated gun and it only takes about a 2 second shot to fill them. I plan to change the two upper axle joint zerk fittings to 90º. Due to clearance issues, It will make greasing those two joints easier than with the straight fittings.
This is the final product. I tested the articulation on a steep driveway at the storage yard and all appears to be OK. An extended road test is still waiting to be done.
I may paint the faces of the two ends visible on either side between the rear tires. The yellowy finish is kind of bothering me.
Anyway, another upgrade job I am glad I tackled.

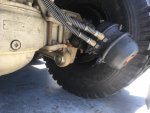
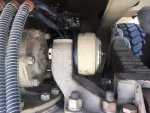
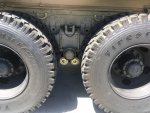
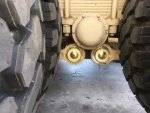
Last edited: