joshuak
Active member
- 747
- 214
- 43
- Location
- Slower shore, DE
Cordial greetings moderators, fellow members and guests. I humbly present for your viewing pleasure,frustration,whatever, how I am embracing my recently acquired MV addiction. I acquired it unknowingly when I purchased an M1009, with the intention of using alternative fuel, but what I've discovered is so much more than that. The fun I've had this past 3/4 of year with my vehicle can only be understood by fellow enthusiast. It been a blast and I would like to share.
I come from a general labor, Environmental Engineering, current WWTP operator back ground. Not much to choose from for this particular endeavor, most of the work displayed was learned on the fly, excuse what some may consider, not proper technique. All I can say is: I'm getting her done.
Here is the willing patient, on the way home from recovery, about 6 hours away from home. So glad I did not turn her off or she turned off be herself, I would have been in a pickle, PO used a heavy duty charger to start and my recovery equipment consisted of tire changing equipment located in my wife’s Yaris (support vehicle). Didn't think about it at the time, somewhat irresponsible. Legal documents: bill of sale and insurance, at least I had that going for me.
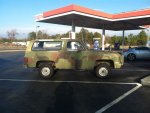
I come from a general labor, Environmental Engineering, current WWTP operator back ground. Not much to choose from for this particular endeavor, most of the work displayed was learned on the fly, excuse what some may consider, not proper technique. All I can say is: I'm getting her done.
Here is the willing patient, on the way home from recovery, about 6 hours away from home. So glad I did not turn her off or she turned off be herself, I would have been in a pickle, PO used a heavy duty charger to start and my recovery equipment consisted of tire changing equipment located in my wife’s Yaris (support vehicle). Didn't think about it at the time, somewhat irresponsible. Legal documents: bill of sale and insurance, at least I had that going for me.
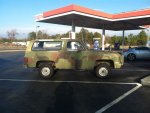