The Caswell Plating is a process that is true zinc electroplating. The kit comes with the chemicals create a bath that efficiently allows the current to flow from a sacrificial zinc plate (neg)(99% pure zinc) to the part (pos). Once a part is plated with zinc it is dipped in the chromate dye. The dye absorbs into zinc, without zinc the chomate dye just washes off. With that said, the cast aluminum has some zinc content. It isn't pure aluminum. It is my understanding that the aluminum can be zinc plated in addition to the zinc it already has but based on my limited research this wasn't done in the original manufacturing process. The aluminum was just chromate coated and the chromate reacted to the zinc in the casting. I did the following....
Aluminum parts -
1. Cleaned with standard carb solvent.
2. glass beading
3. full degrease with brake cleaner.
4. Dip in hydrochloric 5% Water 95% for about 5-10 sec.
5. Rinse with R.O. Water
6. Dip in Caswell Chromate dye yellow. Note - Black and OD available.
The above process created what I think is the original color based on what I observed under the unexposed gasket areas before bead blasting. From what I have read a more modern restore would require a zinc plating to the aluminum before chromate. This should create a bright yellowish finish on the aluminum. I think it would base on some experience I did over 30 years ago when restoring carbs on 60-70's Mopar carbs with products similar to Caswell. Not what we want on a military restore.
Metal parts -
1. Cleaned with standard carb solvent.
2. glass beading
3. full degrease with brake cleaner.
4. Zinc plate - 1.5-2 volts. Current adjusted enough to see bubbles forming like foam on the surface. 15min.
5. Rinse with R.O. Water
6. Dip in Caswell Chromate dye yellow. Note - Black and OD available.
Metal parts are the same as aluminum but required the parts to be re-zinced since the blasting and years of corrosion removed all the original zinc plating. I'm not sure how shining the metal parts would have been originally. If you polish the metal before zinc plating you will get a more shinny plate. I choose not to polish but I think a slight polishing would have yielded a more accurate finish. The stamped out part originally wasn't polished but I think the natural finish of a new stamping wouldn't have been matte like my bead blasted parts. If I do anything over I would polish the metal parts to a sheen and then zinc plate.
Below is the finished results
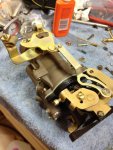
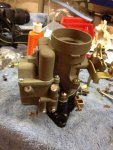
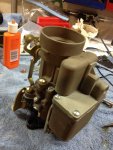
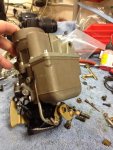
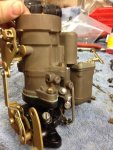
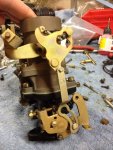
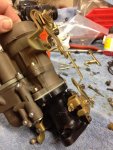