- 1,159
- 1,344
- 113
- Location
- Basehor, KS
As announced in a separate post several weeks ago, Larry @Cowhunter and myself have started on converting his 005A to a MeBay DC-70DR MK II controller based system
we will update this thread here over the next several weeks
Larry and his 005A are based in Southern California and I am in Kansas City. I am doing this remotely.
Why are we doing this?
Larry had his 005A converted to single phase zigzag as per instruction videos on YouTube from one of our infamous members, to power his workshop primarily
Larry ran into the same issues as most other folks who did the single phase conversion, namely setting the output voltage to 240VAC between the two phases, winding up with two blown A11 static exciter voltage regulators.
I have repaired both and they are running fine now.
As a general piece of advice:
Because the A11 can be adjusted to 240VAC, which is pretty much the top end of regulation, doesn’t mean that they should be set that high.
The 004A / 005A / 006A are RATED for 208 VAC and so this A11 in all three units. The same goes for the Tactical Precise Version.
During the course of the A11 repairs, I realized that Larry’s cubicle has seen much better days as nature had delivered a pretty good beating on this nearly 50 year old piece of equipment.
So the idea was born to strip all the old electronics out and start fresh.
After evaluating several modern day controllers, like the British made Deepsea controllers, Larry decided to go with a more economically priced Controller from MeBay, bought on Amazon and shipped from China.
the DC 70 DR MK II costs just around $ 200
Larry then sent the controller to me for programming
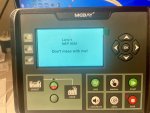
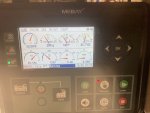
we will update this thread here over the next several weeks
Larry and his 005A are based in Southern California and I am in Kansas City. I am doing this remotely.
Why are we doing this?
Larry had his 005A converted to single phase zigzag as per instruction videos on YouTube from one of our infamous members, to power his workshop primarily
Larry ran into the same issues as most other folks who did the single phase conversion, namely setting the output voltage to 240VAC between the two phases, winding up with two blown A11 static exciter voltage regulators.
I have repaired both and they are running fine now.
As a general piece of advice:
Because the A11 can be adjusted to 240VAC, which is pretty much the top end of regulation, doesn’t mean that they should be set that high.
The 004A / 005A / 006A are RATED for 208 VAC and so this A11 in all three units. The same goes for the Tactical Precise Version.
During the course of the A11 repairs, I realized that Larry’s cubicle has seen much better days as nature had delivered a pretty good beating on this nearly 50 year old piece of equipment.
So the idea was born to strip all the old electronics out and start fresh.
After evaluating several modern day controllers, like the British made Deepsea controllers, Larry decided to go with a more economically priced Controller from MeBay, bought on Amazon and shipped from China.
the DC 70 DR MK II costs just around $ 200
Larry then sent the controller to me for programming
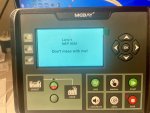
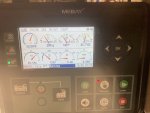
Last edited: