THE WIRING... Old thread I know, but I didn't want to add another thread to the mix, and sorry I didn't take pics along the way... Unless your existing wiring already has the twist-lock type pump connector, I really suggest that the pigtail from the new pump be
soldered to your old power lead. For those of us who haven't soldered for awhile (or ever) Chris Fix has a great 12 minute tutorial video here;
https://www.youtube.com/watch?v=Zu3TYBs65FM
When I did mine, I carefully/barely cut through and removed the shrink tubing from the new pump's pigtail, and removed the white ground wire from the pump. Then I pushed the woven shielding back to expose the power lead, and stripped the insulation back about 3/4" from the cut end. On the old pump's lead, after I dried off all the fuel from the pump and lead, I used a dremel with an abrasive disc to just barely cut through the pinch clamp on the pump end, then pried off the pinch clamp, pushed the woven shielding back to expose the wire, cut off the connector/pump, and stripped that lead back about 3/4" also. Next, I slipped a 3" long x 3/8" piece of shrink tube over the old cable's shielding. Then I slipped a 2" piece of 1/4" synflex brake hose over the wire itself, followed by a 1-1/2" long x 5/32 piece of shrink tubing. I then soldered the new pig tail lead to the old cable lead, slipped the 5/32 heat shrink over the joint, and shrunk it with a heat gun. Next, I slipped the 1/4" synflex over the newly soldered/shrink-tubed joint, and worked the shielding from both ends over the synflex to touch in the middle of the synflex. Once the shielding was covering the snyflex, I slipped the 3/8" shrink tube over the joint in the shielding, and shrunk it in place with the heat gun (
the synflex and additional layer of heat shrink may sound like overkill, but the thought of arcing in any fuel tank gives me the willies. I beleive this is one of those times in life where some redundancy is a very good thing!). For the ground wire, I just used the one from the old pump because it already had ring teminals soldered to both ends. One end stays connected to the pump bracket, the other end connects to the terminal on the top of the new pump where the white wire was removed. That should be about it. My positive lead and the connections going into my fuse box were getting loose and crunchy, so I cut the lead back, and replaced the ring terminal on that end as well. That's why you see the shrink tubing at the top of the lead, and the new fuse box on top of the mount flange.
As a side note, If you're going to replace any of the in-tank wire or hose with new, you'll need to get the right stuff... You don't want just any wire or hose taking a constant bath in fuel. That e-auction site has vendors selling 14AWG, PTFE (Teflon) insulated wire for .99 cents a foot, which is what I'd use, and if you plan on replacing the hose, here's good info and a link for hose that's compatible with today's diesel biodiesel/blends, and about any fuel you'd run in your truck; https://www.steelsoldiers.com/showthread.php?177452-In-Tank-
[URL="https://www.steelsoldiers.com/showthread.php?177452-In-Tank-Pump-Hose-For-Deuce"]Pump-Hose-For-Deuce
[/URL]
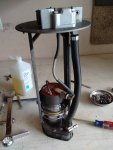
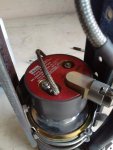
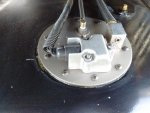