- 488
- 367
- 63
- Location
- California
Maybe this was discussed before and I couldn't find anything about it...I am not a mechanical engineer, but looking at the way the 200A alternator is attached to the driver side cylinder head (I am talking about the 6.5L, but maybe it's the same on the 6.2L), it doesn't feel right.
Statically the weight distribution could be OK as most of the weight could be taken by the lower bracket (#4), given that the 3 bolts (#9 & #10) on the cylinder head were tighten after bolts #1 and #16 under the alternator, on the bracket attached to the engine block. Either way there will be constant stress if the bracket is made slightly on one extreme of the tolerance, but if the 3 bolts (#9 & #10) are tighten last, any potential play around them will go towards alleviating the bracket push or pull stress instead of adding to it.
And dynamically, things appear a lot worse...if you look at the longer twisted bracket under the alternator, which is almost twice the length of the upper bracket and with only one support point vs three, it seems that it would have a lot more flex than the heavy bracket on the cylinder head, meaning that when driving over bumps and rough terrain, the alternator will try to bounce up and down (let's leave aside any longitudinal and lateral forces during accelerating, stopping and turning and focus just on the Z axis for now) due to its heavy mass and all the flex in the lower bracket (#4) will get transmitted via the 3 bolts (#9 & #10) on the cylinder head and get absorbed mostly by the front TTY bolts closer to the first 2 cylinders and maybe the third.
The stress would increase significantly if the lower bolt(s) #1 and/ or #16 securing the alternator to the block bracket #4 (bracket #3 is not present on my truck serial # over 300k) ) would get even slightly loose as then even more of the alternator mass will get transferred to the front cylinder head bolts trying to pull them upwards everytime when going over bumps.
With the constant up and down (Z axis) vibration, over time, I can see how the front area of that cylinder head TTY bolts could start giving in, making it easier for the gasket to leak in that front corner. Unless I am missing something, I would think that trucks with the heavier 200A alternators (and maybe the 400A too if are secured the same way) are more prone to having this issue and maybe it happens more frequent on those engines/ alternator combinations.
I would prefer for the whole alternator to be supported only by the block without applying any additional stress to the cylinder head, which is already under a lot of pressure at higher RPMs.
Or at a minimum, the 3 bolts (#9 and #10) should be secured with shoulder washers/ spacers that would have some type of sprung play equivalent with the [ lower bracket flex + potentially loose screw #1] combined play.
But ideally, that alternator should be secured directly to the engine block, not via the cylinder head TTY bolts.
Is my thinking in the woods?
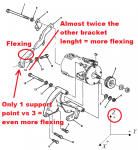
Statically the weight distribution could be OK as most of the weight could be taken by the lower bracket (#4), given that the 3 bolts (#9 & #10) on the cylinder head were tighten after bolts #1 and #16 under the alternator, on the bracket attached to the engine block. Either way there will be constant stress if the bracket is made slightly on one extreme of the tolerance, but if the 3 bolts (#9 & #10) are tighten last, any potential play around them will go towards alleviating the bracket push or pull stress instead of adding to it.
And dynamically, things appear a lot worse...if you look at the longer twisted bracket under the alternator, which is almost twice the length of the upper bracket and with only one support point vs three, it seems that it would have a lot more flex than the heavy bracket on the cylinder head, meaning that when driving over bumps and rough terrain, the alternator will try to bounce up and down (let's leave aside any longitudinal and lateral forces during accelerating, stopping and turning and focus just on the Z axis for now) due to its heavy mass and all the flex in the lower bracket (#4) will get transmitted via the 3 bolts (#9 & #10) on the cylinder head and get absorbed mostly by the front TTY bolts closer to the first 2 cylinders and maybe the third.
The stress would increase significantly if the lower bolt(s) #1 and/ or #16 securing the alternator to the block bracket #4 (bracket #3 is not present on my truck serial # over 300k) ) would get even slightly loose as then even more of the alternator mass will get transferred to the front cylinder head bolts trying to pull them upwards everytime when going over bumps.
With the constant up and down (Z axis) vibration, over time, I can see how the front area of that cylinder head TTY bolts could start giving in, making it easier for the gasket to leak in that front corner. Unless I am missing something, I would think that trucks with the heavier 200A alternators (and maybe the 400A too if are secured the same way) are more prone to having this issue and maybe it happens more frequent on those engines/ alternator combinations.
I would prefer for the whole alternator to be supported only by the block without applying any additional stress to the cylinder head, which is already under a lot of pressure at higher RPMs.
Or at a minimum, the 3 bolts (#9 and #10) should be secured with shoulder washers/ spacers that would have some type of sprung play equivalent with the [ lower bracket flex + potentially loose screw #1] combined play.
But ideally, that alternator should be secured directly to the engine block, not via the cylinder head TTY bolts.
Is my thinking in the woods?
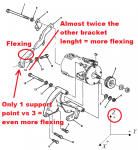
Last edited: