gimpyrobb
dumpsterlandingfromorbit!
- 27,786
- 765
- 113
- Location
- Cincy Ohio
So I've had a couple of push/pull mig units for a while. Now that I have an Al flat bed on my pickup, I'd like to add stake pockets and a rub rail to the sides. Of course, that comes after I weld on the rear C channel cause I shortened the bed a tad. Here is a couple pics of my first Al welds, I know - no big deal, but its exciting learning a new process! If anyone has any old Cobramatic stuff laying around, I'd be interested in it!
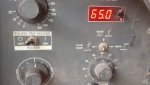
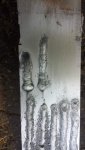
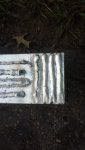
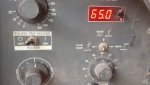
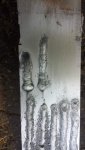
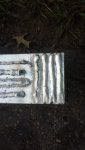