No problem. I share your aversion to heat. I spent most of my high school years trying to keep a 1967 Austin Cooper S alive. Heat, it always comes down to too much heat. The Mini is currently in pieces while I wait for the machine shop to do some work. Heat again a few years ago.
Which leads into the next part of my Cowdog tale....
My engine is a 6.5 GEP pull out. The tag said it was overheated. Some new still in the packing crate/tin foil GEP center mount turbo 60° intake bolt heads came with the engine. I really debated with myself about what to do. Refurbish the stock 6.5 NA heads that had I think the T pre cups and 90° intake bolts, set up a set of stock 6.2 heads or throw on the diamond pre cup 60° intake bolt heads? Heat was my main reason to do with the center mount turbo heads.
With these non direct injection engines the fire is started in the pre combustion chamber off to the side in the cylinder head. The fire then spreads through the throat to over the piston. The small throat 6.2 engine got great mpg's, were kind of quiet and responded well to a turbo with modest power gains. Try to get what is now considered normal power and the small throat heads get hot. Very, very hot real fast.
GEP reworked the coolant passages in the cylinder heads a little, used different metal and put bigger throat pre cups in the non turbo heads. They probably would have worked fine for my needs. But I figured if I am building an engine I might as well try to get the most out of it. On went the diamond pre cup heads with the biggest throats ever made for a 6.x. Except maybe the P400 engine.
The problem with using those heads is the intake manifold mounting. All of the 6.2 and 6.5 NA or turbo engines up until the 2000 center mount turbo engines had intake manifold bolts that were 90° to the intake face of the head. Which means when the intake was installed and the bolts were in. They were angled into the heads. To make it so an intake manifold could be pushed straight down onto a turbo charger the bolts had to also be vertical or 60° to the intake face of the heads.
Way back in 2016 I couldn't find any of the P van engine or HMMWV engine 3 piece intake manifolds that are supposed to go on the 60° heads. When one did come up it was usually missing one of the 3 pieces or was so expensive I didn't even give it serious thought. So I modified a CUCV 6.2 intake to work with the center mount turbo heads. Post #88 of this thread shows that process.
While doing my research about boost, fuel rates, EGT and their relations I stumbled across the world of boost leaks and boost leak test. So I collected what I needed to do a boost leak test. Here is what I found:
I started looking for the 3 piece center mount turbo intake set up. I finally found a complete set up back in October that was priced at $100 because someone had tapped and plugged a sensor hole in a not visually pleasing way. I could care less about those looks. Once it made it to my door I had to figure out how to make it work with my turbo.
Here is what the assembly looks like:
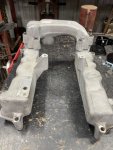
That hole in the cross over piece is 2.87 inches diameter. It is supposed to just slip over the output nozzle of the center mount turbo. My turbo sits outside the passenger side head down even with the exhaust ports. 2.87 doesn’t match up to any piping I could find. Something had to be made. The Banks turbo outlet pipe is 2.5 inches outside diameter.
I found a 2 foot section of .50 wall 3 inch OD 2.5 inch ID aluminum pipe. I have a 1927 South Bend lathe that collects dirt and dust most of the time. But, I cleaned it up, oiled everything and chucked up the pipe. I cut off an 8 inch section and then turned one end down to 2.82 inches. I also purchased a 6.5 center mount turbo output O-ring. That O-ring was way too thick to work on my pipe. But, I tried by turning a .5 inch section down to 2.70. The factory O-ring still wouldn’t fit. With no more aluminum left to cut I put 2 #30 O-rings in the groove and that worked perfectly.
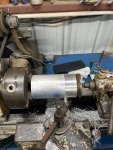
I only have 1 O-ring in the picture. Then I drilled and tapped 3 holes in the cross over plenum to put set screws in for holding the aluminum pipe in place under pressure and vibration.
Next was a 3 inch ID to 2.5 inch ID 120° silicone conversion boot. A 6 inch aluminum 2.5 inch OD straight section of inter cooler piping was next. I had to do a lot of searching of Tuner parts houses to find all of this stuff. It seems the WRX and Supra crowd love to make miles long intercooler plumbing so parts are plenty and really very cheap. Then a silicone 2.5 inch to 2.5 inch 90° elbow got me to where I thought it would meet up with the Banks aluminum piping. Another 6 inch straight section was needed too.
Here is how it looked all assembled and mocked up:
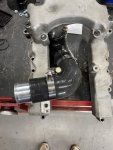
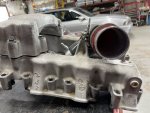
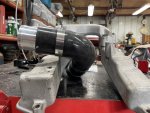
I also drilled sand tapped a hole in the turned aluminum pipe for a boost gauge hook up. I thought I had screwed myself over with the set screws. The had to be below the O-rings to maintain a good seal. Pushing the really tight O-rings past the drilled and tapped holes cut the O-rings. Silicone spray ate 2 more. Grease ate another pair. I ended up putting painters tape over the holes and dousing everything with silicone to get it successfully together.
Once I had the old manifold off, everything on the engine clean and new gaskets in place. The manifold runner on the passenger side didn’t want to go on because the #6 and #8 injector lines along with the fuel supply line to the fuel filter and the hose from the filter to the IP all pile up high enough to block the manifold runner. I messed with it a bit and got it to fit. Then, I found out my aluminum pipe set up was about a half inch too long. Thankfully the silicone boot compressed enough to let everything bolt on and get snugged down. Meaning I probably could have done without the set screws and all of their related issues. Next time.
I have been driving with this set up for about 2,000 miles now. Boost is about a half pound to a pound higher in steady cruise. EGT is down 50° to 100° due to the increased airflow no leaks means. We have very few hills here. But, with the cruise set on what we have the truck doesn’t down shift on hills it always has downshifted on. Jumping to 5-6 psi boost and just grunting its way up with no drama. I now have the WMI set to start at 5 psi because I can hit 4 psi just getting up to highway speeds with slight throttle. All in is 8 psi which is reached anytime I get more than 50% throttle. But it really spends very little time that high of boost now because the speed is already there.
MPG has gone up as well. 16-19 is now common instead of a once in a while thing.
Here is what it looks like on the engine:
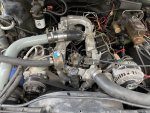