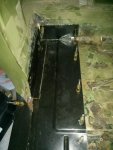
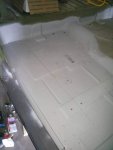
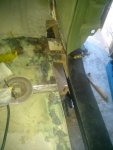
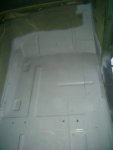
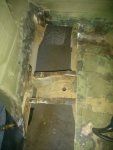
Its been a while since my last post but I've been chipping away at the passenger side floor so here is an update.
The rot wasn't as bad on this side as the drivers side but it seemed more wide spread if that makes sense. Small areas of rot dotted the kick plate area and the door threshold along with the rocker panel. So instead of dotting the whole interior with 2x2 inch doublers I decided to cut out large areas and install a lap repair in the same manner as the drivers side.
The removal of the damaged areas was identical to the drivers side so I won't bore you guys with rehashing the specifics. I did manage to NOT cut through the frame supports this time

The only thing I did slightly different was using 3M's Panel Bonder instead of SEM weld-bond. It seemed to have a longer working time before beginning to set which alowed me time to install the hardware with out rippling the repair panel.
I fablicated the repair parts for the rear corner and kickplate areas from the remaining portions of the drivers side floor pans that went unused. Then I cut out the needed patches from passenger side floor pans ordered from RockAuto.com, Leaving two inches of over lap for good adhesion and stainless fasteners. Drilled, cleco'd, removed, deburred, primed, installed and edge sealed.
The next day was dedicated to treating the remaining surface corrosion with a grinder, wire wheel and Rust-olium reformer. Let dry for 24 hours then applied two coats of gray primer.
Now its on to the rocker panel which is epoxied in place just needs to be faired in.