- 1,450
- 123
- 63
- Location
- Gray, GA
Before I get started I must give credit where it's due. Throughout this process, 74M35A2 has been an infinite source of knowledge on the specifics and details of this alternator. He stayed with me from the purchase, to when I fired it up after I was done. Without him, I'd still be using trial and error to make this work, which we all know can be costly and time consuming.
Alternator details:
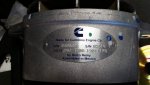
This is a New Genuine Delco Remy 33si brushless alternator rated for 24v and 100A [NSN 2920-01-484-9161 - P/N 3400698]. It was designed for severe duty applications, like heavy equipment, and has features that help prevent moisture, dust, corrosion and heat damage. It is right at 5 pounds lighter than the stock alternator and is also shorter, as seen in the comparison picture below. It is temperature compensated and uses a single wire connection, although there are provisions for other configurations there too.
This will not be an economical upgrade for most folks since the price of these is on the high side. These were used on a few MVs though, so they can be found in surplus, which is where I got mine. Buying one straight from a civilian dealer would not be very cost effective. I decided to upgrade mainly due to the Warn winch I use. Everything is LED on the truck so the winch is the only real load. The high failure rate of the factory alternator never left me with a warm fuzzy feeling that it'd be there when I needed it most.
The install:
This is a comparison picture between new and old. I placed them with the pulleys square to each other to give an idea of the differences. The pulley will have to line up so everything else will have to fall in line. I also have the bracket lined up so you can see what will need to be adapted to make it work. I didn't find a bolt on bracket that would work so I went the modification route.
The bolt holes on the engine side of the bracket are slotted. With the factory alternator the bracket is all the way to the back. With the shorter shaft on the new alternator the bracket will need to be all the way forward to line things up.
The original bracket is a long version and the alternator needs a short one, so spacers will have to be used. The original holes are smaller, maybe 5/16" bolts, and the new alternator uses 1/2" bolts so the holes will need to be drilled out on the alternator side of the bracket. I then used some 1/2"ID x 3/4"OD seamless round stock to make a rear spacer. I used this so there would be plenty of meat for a solid weld to the bracket. A long bolt is used on the rear ear and a standard length bolt is used on the front with no spacer. This places the alternator in alignment with the drive pulley.
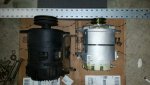
The tension bar will have to be drilled to 1/2" too. I flipped the bar around and drilled the hole instead of the slot. This was much easier to do. The adjustment end is now on the engine side of the bar. A spacer will also be needed here to keep the bar square to everything else. I welded the spacer to the bar using the same material as the rear spacer.
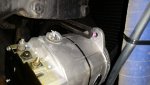
Since the new pulley is a smaller diameter, some shorter belts will be needed.
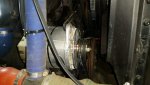
Trial and error on belt sizes. The washers on the tension bar have since been replaced with a welded spacer.
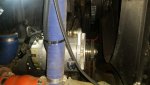
The positive wire goes to the POS terminal and the ground wire goes to the case.
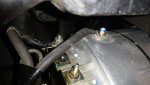
The finished product. This was during a test run. The bracket and tension bar now have the spacers welded in place.
https://youtu.be/Du7vdp9uhQg
If you happen upon one of these for a good price then it's not a bad install. You'll end up with a quality severe duty alternator you'll never question again.
Cost analysis:
Alternator -$70
Pulley - $13.50
Shorter matched V-belts - $14.00
Misc. - $20
Total - $117.50
Alternator details:
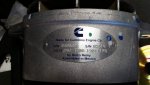
This is a New Genuine Delco Remy 33si brushless alternator rated for 24v and 100A [NSN 2920-01-484-9161 - P/N 3400698]. It was designed for severe duty applications, like heavy equipment, and has features that help prevent moisture, dust, corrosion and heat damage. It is right at 5 pounds lighter than the stock alternator and is also shorter, as seen in the comparison picture below. It is temperature compensated and uses a single wire connection, although there are provisions for other configurations there too.
This will not be an economical upgrade for most folks since the price of these is on the high side. These were used on a few MVs though, so they can be found in surplus, which is where I got mine. Buying one straight from a civilian dealer would not be very cost effective. I decided to upgrade mainly due to the Warn winch I use. Everything is LED on the truck so the winch is the only real load. The high failure rate of the factory alternator never left me with a warm fuzzy feeling that it'd be there when I needed it most.
The install:
This is a comparison picture between new and old. I placed them with the pulleys square to each other to give an idea of the differences. The pulley will have to line up so everything else will have to fall in line. I also have the bracket lined up so you can see what will need to be adapted to make it work. I didn't find a bolt on bracket that would work so I went the modification route.
The bolt holes on the engine side of the bracket are slotted. With the factory alternator the bracket is all the way to the back. With the shorter shaft on the new alternator the bracket will need to be all the way forward to line things up.
The original bracket is a long version and the alternator needs a short one, so spacers will have to be used. The original holes are smaller, maybe 5/16" bolts, and the new alternator uses 1/2" bolts so the holes will need to be drilled out on the alternator side of the bracket. I then used some 1/2"ID x 3/4"OD seamless round stock to make a rear spacer. I used this so there would be plenty of meat for a solid weld to the bracket. A long bolt is used on the rear ear and a standard length bolt is used on the front with no spacer. This places the alternator in alignment with the drive pulley.
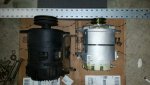
The tension bar will have to be drilled to 1/2" too. I flipped the bar around and drilled the hole instead of the slot. This was much easier to do. The adjustment end is now on the engine side of the bar. A spacer will also be needed here to keep the bar square to everything else. I welded the spacer to the bar using the same material as the rear spacer.
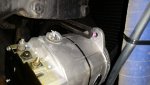
Since the new pulley is a smaller diameter, some shorter belts will be needed.
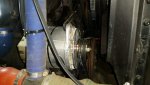
Trial and error on belt sizes. The washers on the tension bar have since been replaced with a welded spacer.
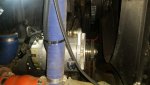
The positive wire goes to the POS terminal and the ground wire goes to the case.
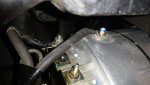
The finished product. This was during a test run. The bracket and tension bar now have the spacers welded in place.
https://youtu.be/Du7vdp9uhQg
If you happen upon one of these for a good price then it's not a bad install. You'll end up with a quality severe duty alternator you'll never question again.
Cost analysis:
Alternator -$70
Pulley - $13.50
Shorter matched V-belts - $14.00
Misc. - $20
Total - $117.50