Demoh
Member
- 217
- 26
- 18
- Location
- St Pete, FL
So ive been going through an 831 in the spare time while I wait for parts to come in for my 803s, and aside from the unit being close to mint with a 12 hour engine, This unit has an overvolt condition. L1 - L2 is over 400 volts, L1 - N is 200+ and L2 - N is the remainder.
Alternator on all 4 phases/poles and all 3 windings on each phase test good including the charging coil. Roughly 200vac on my backup "I cant find my meter, I guess this will do" harbor freight meter, 15 ohms per coil for the HV side. Potentiometer sweep seems within spec, its a 0-5k pot right? Im not quite getting 5k out of it but I blame the meter.
Ive done all of the pertinent tests in the TM so I ended up pulling A8 out of the unit and fully disassembling it. Looks like the depot threw in a unit pulled from the sand dunes overseas and then ran it until it got submerged in water. I cant find any traces of magical smoke being let out anywhere so I think if I just give this unit some TLC, test the components I can test, and reassemble I should be good.
Does anybody have experience rebuilding these units? These look super simple except the logic board and whatever issue I have with an overvolt is going to be either a bridged HV trace, the sense circuit so the logic doesnt know how high it is, or the actual drivers doing the work. Either way this shouldnt be much different than the CNC spindle driver that I rebuilt in my milling center. (That unit has a firmware and a lot more complexity to it though)
I will say I am very impressed in the robustness of this module. Definitely feels overengineered compared to my mill stuff and the 20-50 kva 3 phase battery backups that I worked on in the past. (The UPS the size of a half height server rack cabinet that Ive worked on the internals seems more like cracker jack box components compared to this thing.)
Of course it wouldnt be any fun without pictures. Also I tasted the dust, it tastes just like the dust in my 803 that came from Kuwait. Does anybody know if all of the dust over there tastes the same?


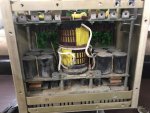
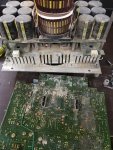
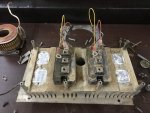
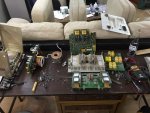
Alternator on all 4 phases/poles and all 3 windings on each phase test good including the charging coil. Roughly 200vac on my backup "I cant find my meter, I guess this will do" harbor freight meter, 15 ohms per coil for the HV side. Potentiometer sweep seems within spec, its a 0-5k pot right? Im not quite getting 5k out of it but I blame the meter.
Ive done all of the pertinent tests in the TM so I ended up pulling A8 out of the unit and fully disassembling it. Looks like the depot threw in a unit pulled from the sand dunes overseas and then ran it until it got submerged in water. I cant find any traces of magical smoke being let out anywhere so I think if I just give this unit some TLC, test the components I can test, and reassemble I should be good.
Does anybody have experience rebuilding these units? These look super simple except the logic board and whatever issue I have with an overvolt is going to be either a bridged HV trace, the sense circuit so the logic doesnt know how high it is, or the actual drivers doing the work. Either way this shouldnt be much different than the CNC spindle driver that I rebuilt in my milling center. (That unit has a firmware and a lot more complexity to it though)
I will say I am very impressed in the robustness of this module. Definitely feels overengineered compared to my mill stuff and the 20-50 kva 3 phase battery backups that I worked on in the past. (The UPS the size of a half height server rack cabinet that Ive worked on the internals seems more like cracker jack box components compared to this thing.)
Of course it wouldnt be any fun without pictures. Also I tasted the dust, it tastes just like the dust in my 803 that came from Kuwait. Does anybody know if all of the dust over there tastes the same?



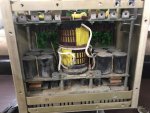
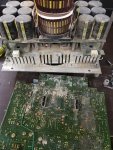
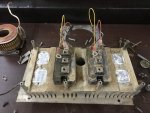
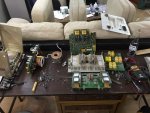