Been thinking about the electric hydraulic pump that runs the liftgate when the truck engine is off. It is set up to run on 3 phase power when a generator is attached to the truck for power. Since i do not have a 3 phase generator to do that i though about converting the pump to single phase power or 24 volts. Since I plan to use the liftgate as a work platform here at home I thought single phase would be the least expensive way to go.
Yesterday I removed the pump and sealed off the hydraulic feeds to and from the pump. This allows me to still use the liftgate with PTO power. The electric pump was tapped in parallel to the PTO pump. The pump also had a badly cracked hydraulic hose going to it. I will replace it when I reinstall the pump assembly.
Once I removed the pump I used paint stripper and scraper to remove the paint off the data plate of the motor to determine the specifications of the motor. Basically its a 2HP 3 Phase motor. It has (4) 3/8" bolts securing the pump to the motor. Here is the data plate:
Here are some pictures of the motor/pump setup:
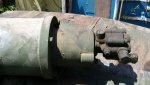
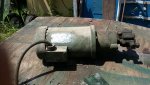
When i had a chance last night I searched on Ebay (6500 listings) looking for a single phase replacement motor. After hours of looking I found 1 that matched my specifications. It looks like it will be a direct match (no modifications required.) I negotiated a good price on it. ($203.17 shipped) Here are some helpful pictures and specs on the motor:
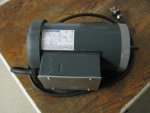
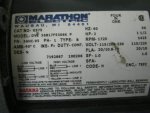
I will update this entry once I receive the motor and attempt to hook up the pump.