85CUCVtom
Active member
- 712
- 26
- 28
- Location
- Lakewood, Ohio
So I replaced my ball joints today and I followed the install instructions in the TM pertaining to the upper ball joint adjusting sleeve but I feel like something is wrong here. The adjusting sleeve seems deep in the knuckle and a lot of threads are visible. I followed the torque instructions to a "T" in the TM, but I don’t want to just assume that this is right.
I checked my part numbers multiple times and everything looks good. Maybe the part is out of spec? They are Moog brand ball joints- I have t had any issues in the past with their parts. Let me know what you think.
Edit- I just thought of this; would the ball joint shaft turning as you tighten the adjusting nut cause this? Like maybe the nut goes too deep before achieving the torque spec?
Take a look:
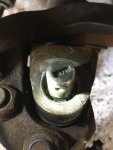
I checked my part numbers multiple times and everything looks good. Maybe the part is out of spec? They are Moog brand ball joints- I have t had any issues in the past with their parts. Let me know what you think.
Edit- I just thought of this; would the ball joint shaft turning as you tighten the adjusting nut cause this? Like maybe the nut goes too deep before achieving the torque spec?
Take a look:
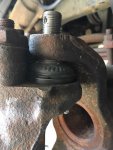
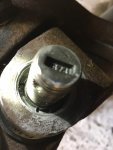
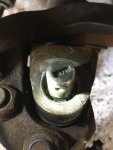
Last edited: