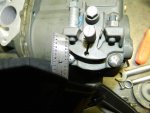
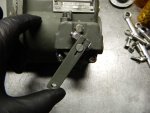
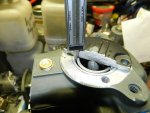
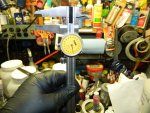
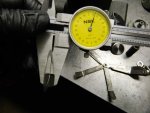
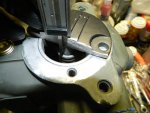
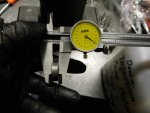
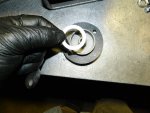
Now to install the governor springs and shims.
Picture 1 shows the operating shaft assembly adjusted. Preliminary adjustments are to set both screws to 5/32".
Picture 2 shows how the operating lever is to be positioned (idle) for taking the governor springs shim measurements.
Picture 3 is taking the measurement for the outer spring, which will have a finished gap of 0.059" .
Since I had a measurement of 0.070" (pic 4) I used a 0.010" shim (pic 5) .
Picture 6 is taking the measurement of the inner spring, which will have a finished gap of 0.158" .
Since I had a measurement of 0.433" I used a 0.275" shim (pic 7) .
Picture 8 shows the shims needed and picture 9 shows them installed along with the gasket. I then installed the cap and bolted it down.
Note: If you make your own "gage" like I did, be sure to add 0.010" to your measurements for the thickness of the gasket.