rsl0311usmc
Member
- 83
- 70
- 18
- Location
- NC
Alright guys I have been replacing a good amount of stuff on the front end here lately from the drag link to wheel bearings, spindle bearings, and axle shaft u joints on both sides. The other day I luckly came across a really bad axle shaft u joint that literally has no needle bearings in the cap and a ton of play. I am shocked it didn't let go. Thankfully I contacted hillbilly wizard and I got all new bearings and seals on the way. I am glad he advised me to get the spindle bearing because when I took it apart one of the needle bearing was missing and it fell apart. I got everything cleaned up and the races out. My biggest question is in all the information I have gathered I am still unsure of final torque specs for these nuts that preload the bearing and hold the spindle. My assumption is the one with the divet threads on and while turning the hub you do 50 ftlbs torque then loosen and spin while seating it again at 50 ftlbs. Then you back it off 90 degrees and slide the washer with the holes in it on making sure to get everything lined up. Finally you put the last locking nut on and torque to 50 ftlbs or is it more? I have heard up to like 150 or 120 ftlbs I think it was and that seems like alot. Thanks again everyone for any information you can give me.
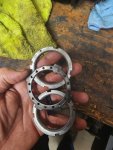
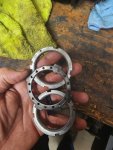