wcuhillbilly
Member
- 421
- 7
- 18
- Location
- Devils Tower, WY
Got the shaft back from my machinist, the shaft fought him and he ended up breaking a few end mills from it hopping out of the cradle, then while cutting the splines his mill got out of sequence, thus--- start over. Prices thus far, machining-$580. Drive line shop flanges/yokes/joint. $150 so this venture has cost me a bit over $700.
Got it back in tonite but need to cut some more out of the crossmember.
Here are some pics of the shaft
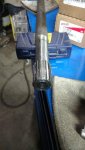
Welded up old 12 spline and cut in modern 16 spline (no 12 spline yokes made anymore)
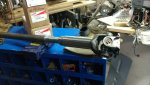
High angle 1330 yoke, flange, on shaft.
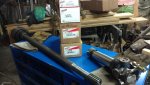
Part numbers
part numbers didn't come through on the pic as well as I had intended, so here ya go
PTO Flange,,,,,,,,,,,,,,,,,,,,,,,,,,,,,,,, Spicer 2-1-1313-8 $Cant remember
shaft side flange of PTO flange,,,, Spicer 2-2-459 $39.46
Slip yoke, high angle,.................. Spicer 2-2-8021KX $47.95
1330(1/2ton GM) U Joint............. Spicer 5-153X ..........$10.00
Got it back in tonite but need to cut some more out of the crossmember.
Here are some pics of the shaft
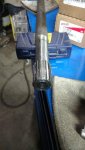
Welded up old 12 spline and cut in modern 16 spline (no 12 spline yokes made anymore)
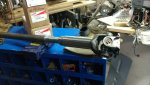
High angle 1330 yoke, flange, on shaft.
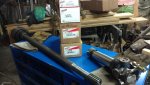
Part numbers
part numbers didn't come through on the pic as well as I had intended, so here ya go
PTO Flange,,,,,,,,,,,,,,,,,,,,,,,,,,,,,,,, Spicer 2-1-1313-8 $Cant remember
shaft side flange of PTO flange,,,, Spicer 2-2-459 $39.46
Slip yoke, high angle,.................. Spicer 2-2-8021KX $47.95
1330(1/2ton GM) U Joint............. Spicer 5-153X ..........$10.00
Last edited: