- 1,394
- 177
- 63
- Location
- Frisco Texas
I installed the side bracket on the back of the condenser, after many blows with a hammer to make it conform to the shape needed. Set it on the tool box (after removing jerry can holder) mark holes and drill. Drill pilot holes in front for bolts. Set in place and cuss and sweat a lot and just before the sun set, it's done!
There is ample room for the frame to twist if going over extreme terrain and not contact the condensor. I know the bed can move, but ... Well, I guess I'll know it if it is too close!
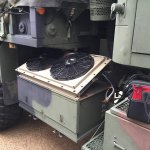
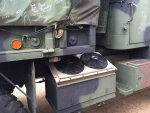
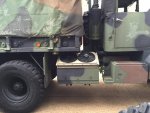
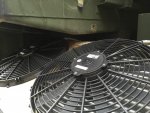
There is ample room for the frame to twist if going over extreme terrain and not contact the condensor. I know the bed can move, but ... Well, I guess I'll know it if it is too close!
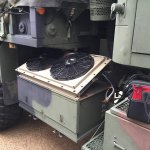
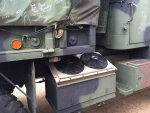
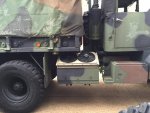
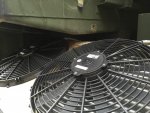