My M37 is done rebuild (engine/transmission) and is running beautifully. I do have an electrical system issue, however. Symptoms include:
Turn signal and headlights are intermittent, but mostly not working. I have not found a pattern to what makes it work vs not work, like jiggling a wire bundle or something isn't yet helping.
Voltmeter is running higher than it used to, but multimeter shows 14.4v at battery and the meter on the dash. Reading on dash meter is something like between 15-16. This may be a non issue.
The headlight dimmer switch fuse heats significantly, melting the plastic on the fuse, but the fuse is not blown
This is a 12v conversion and unfortunately, the TM isn't closely matched since most of these components are different. I do have an M37 wiring diagram and it should be fairly close.
I flipped the dash light switch with a spare I have. but this didn't improve the symptoms.
I am thinking the plastic fuse holder, a blade type block, but I can't see anything obvious there. I dont feel any hotspots (after turning the master off) elsewhere besides the dimmer fuse, and don't see anything obvious elsewhere. The dimmer switch does work when the headlights decide they do want to work, but this may also be a candidate for replacement, its the floor type switch that you step on.
I assume the blinkers and headlights are not working due to a short somewhere the prevents power from reaching them?
Any tips on things to look for in ferreting out this intermittent issue (the worst kind of issue)?
Engine compartment
Ignition and other connections
Delco Remx is model
Foot switch for bright headlights
Turn Signal
Instrument panel
Fuse block
Turn signal and headlights are intermittent, but mostly not working. I have not found a pattern to what makes it work vs not work, like jiggling a wire bundle or something isn't yet helping.
Voltmeter is running higher than it used to, but multimeter shows 14.4v at battery and the meter on the dash. Reading on dash meter is something like between 15-16. This may be a non issue.
The headlight dimmer switch fuse heats significantly, melting the plastic on the fuse, but the fuse is not blown
This is a 12v conversion and unfortunately, the TM isn't closely matched since most of these components are different. I do have an M37 wiring diagram and it should be fairly close.
I flipped the dash light switch with a spare I have. but this didn't improve the symptoms.
I am thinking the plastic fuse holder, a blade type block, but I can't see anything obvious there. I dont feel any hotspots (after turning the master off) elsewhere besides the dimmer fuse, and don't see anything obvious elsewhere. The dimmer switch does work when the headlights decide they do want to work, but this may also be a candidate for replacement, its the floor type switch that you step on.
I assume the blinkers and headlights are not working due to a short somewhere the prevents power from reaching them?
Any tips on things to look for in ferreting out this intermittent issue (the worst kind of issue)?
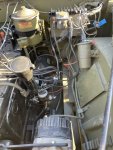
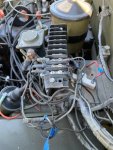
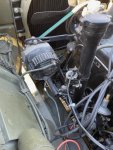
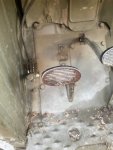
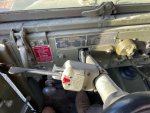
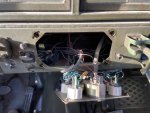
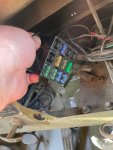