Did some serious thinking about cup holders last night. I searched Ebay, AMAZON.COM, and the internet for heavy duty cup holders. Most of them out there are plastic. They break too easy! Found a Stainless Steel version of the folding cup holder offered in the classifieds. Price was $30 each. Not gonna spend $60 for 2 cup holders! So i start thinking what can i use to make some heavy duty cup holders for the truck? What doe I have in inventory that I can use? Then it came to me! Filter canisters! I did some spin-on filter upgrades on my Deuce, M923, and Diesel Generator set. I knew I had some old canisters out in the shop the i will not need. It was too late last night to go look.
Went out this morning and found a double canister assembly from my generator set. The canisters looked good. There was one short and one long canisters. I removed the short canister from the housing. Went and grabbed a empty soda can to see how the fit would be. It was perfect! Using a tap I threaded the bottom hole for a fine thread 3/8" bolt. There was no drilling required.
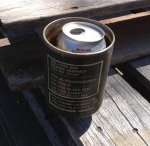
I had thought about using some of the green sleeping bag foam mat as insulator. I cut a piece and tried it for fit. It fit perfect.
Next I decided to see how my new spill-proof cup would fit. It was too tight with the green foam insert. So I brought out some thin insulation I had left over from insulating the Deuce cab. I tried it and it was a good fit. I also wanted to add a bottom drain grate and insulation inside the cup holder. Since the canister had a drain valve I figured I can use it to drain any dripping that ran to the bottom of the canister. I found an old aluminum data plate that had the wiring diagram for the old 15k Generator Head. Using the canister as a template to draw the circle and cut it with some tin snips. I used a punch to make (5) 3/8" holes in the round aluminum piece I just cut. I also punched the holes in the round piece of insulation. I used Scotch 77 spray glue to attach the insulation to the thin aluminum bottom piece.
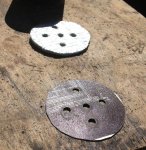
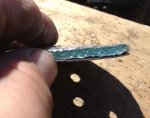
I took the long canister and marked it to match the short canister height. I used a cut off wheel on my angle grinder to cut the canister. I used a Dremil tool with a sanding drum to sand the sharp edge on the cut. I did that to both pieces of the canister I cut. I finished smoothing the edges on both pieces. I tapped the bottom hole for the fine thread 3/8" bolt. I cut another round piece of aluminum for the bottom of the canister. This one will go on the passenger side for the wife to use. Here travel mug is bigger so no room for insulation.
I found one piece of heavy angle and used it for one cup holder. I ran the 3/8" bolt, lock-washer and washer through the bottom of the bracket into the thread hole on the bottom of the cup holder. Looked good and fit nice. I removed it and primed and painted it flat black.
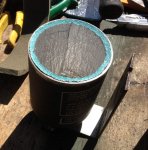
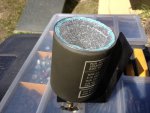