Ronmar
Well-known member
- 4,148
- 7,961
- 113
- Location
- Port angeles wa
I would remove that female QC from the wet tank drain. They are not meant to be out in the weather and will corrode quickly. They also tend to fill up and jam with road grime. Mine gave me nothing but problems, even when I slid a rubber boot over it. i would instead put in a ball valve and a male QC fitting.
A female QC there kind of defeats the purpose of being able to purge moisture from what is supposed to be a filter/separator stage in the system.
A male QC and a ball valve still serve this purpose as well as allowing you to charge or use air from the system. You just need a female-female adapter or female-female hose for the truck that you can keep stored out of the weather when not needed to use air from the truck…
Yours being an A0, I suspect the wet tank is not plumbed into the system correctly anyway. The Wet tank is supposed to act as a secondary cooler/dryer and settling tank so the brakes get the cleanest driest air. In order to serve in this capacity, 100% of the air must pass THRU the wet tank.
Well some bright light at S&S got it wrong, and since the diagrams in the manuals were probably created from the prototypes, they show it wrong in all the manuals that show tank service as well. The only place it is shown correctly is on page 34 of the schematics. Instead of running the air THRU the wet tank, they “T“d the wet tank off the dryer output line to the service tanks. Plumbed like this, i would say less than 1/5 of the brake air ever sees the inside of the wet tank.
Simple mistake, and lucky for us very easy to fix, you simply swap two of the line connections and their end fittings on the wet tank using the hardware thats already there.
Every A1 truck I have looked at is plumbed correctly with 100% of the brake air passing THRU the wet tank…
Here is how it looks from the factory and in the tank service diagrams in the manual.

Here is how it should look, with 100% of the air forced thru the wet tank to get to the brake service tanks.
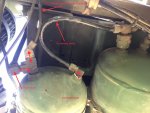
A female QC there kind of defeats the purpose of being able to purge moisture from what is supposed to be a filter/separator stage in the system.
A male QC and a ball valve still serve this purpose as well as allowing you to charge or use air from the system. You just need a female-female adapter or female-female hose for the truck that you can keep stored out of the weather when not needed to use air from the truck…
Yours being an A0, I suspect the wet tank is not plumbed into the system correctly anyway. The Wet tank is supposed to act as a secondary cooler/dryer and settling tank so the brakes get the cleanest driest air. In order to serve in this capacity, 100% of the air must pass THRU the wet tank.
Well some bright light at S&S got it wrong, and since the diagrams in the manuals were probably created from the prototypes, they show it wrong in all the manuals that show tank service as well. The only place it is shown correctly is on page 34 of the schematics. Instead of running the air THRU the wet tank, they “T“d the wet tank off the dryer output line to the service tanks. Plumbed like this, i would say less than 1/5 of the brake air ever sees the inside of the wet tank.
Simple mistake, and lucky for us very easy to fix, you simply swap two of the line connections and their end fittings on the wet tank using the hardware thats already there.
Every A1 truck I have looked at is plumbed correctly with 100% of the brake air passing THRU the wet tank…
Here is how it looks from the factory and in the tank service diagrams in the manual.

Here is how it should look, with 100% of the air forced thru the wet tank to get to the brake service tanks.
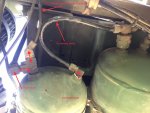
Last edited: