OK, here's another update. Tuesday I got all of the upper hoses from the hard lines to the boom spool, lift and crowd. The pipe/fitting was loose for the crowd out, so I removed it completely to re-seal the pipe. Good thing I did, it was cracked. Woulda made a mess if put into operation, not to mention, a OITA to remove the broken piece in the end of the cylinder.
I got the rest of the lines under the pig disconnected, #8 return and 3 more-16 lines for lift/lower and crane spool in and out. Let that mess sit overnight. It was a tad messy.
This morning, put an extension on the forklift boom, got the lifting part all rigged up and before anyone else got there, decided to give thing a go at lifting the rotating spool out. Took a couple of re-positioning's of the forklift, but got it to where everything cleared. I decided to wait for a bit of help.
When help arrived, I asked him if he was OK with being the lift operator, he was a bit hesitant, but agreed and did a fantastic job! We got the slip spool up out of the center, but the lines were as hard as....well, something on a man's wedding night! After getting the assembly up about 10 inches, it was discovered that the NG unit had installed 2, 8 inch pipe lengths into the return ports of the spool valve. Didn't expect this, but it was a welcome sight even if it did make it so the assembly needed to be raised out of it's place and additional distance. BTW, did some reading, the slip spool assy with nothing else, lines, etc, weighs 120#
One of the lines was EXTREMELY hard, one of the return or down/in ones. We had to disconnect it at the slip. Some people have zero clue. The ....individuals....that assembled this used some sort of locking compound on all of the threads on the -16 lines. Those bastages were freekin tight! With the help of a 36 inch breaker bar, a 1 5/8 open end wrench and a bunch of grunting, the one line we needed to come lood, did. But not without a fight. It was tight to the last thread. After that, all that was needed was to go under it again, guide the rest of the hoses out and pull it out with the forklift. The TM says to remove the boom. PFFFT!
After the assembly was removed, it was clear that the people that had worked on this prior were NOT mechanics. All of the fittings were glued in place, they had been chewed up with a pipe wrench...no clue how that happened as there is no room for one...but the return, -8 line, was almost finger tight. One of the hoses was a bit newer than the others. This is a 1200 PSI system, but a hose that was used was only a rubber outer, woven cotton and rubber inner. You could squish it closed with your hand. I think it was the "boom down" hose.
After removal, it was a bit of a chore to get the lines off of the assembly, bit they went back on easily. I used a bit of Permatex#1 on the threads to prevent leaks, no, it does not harden so the next poor soul that needs to do this won't be cussin' me out. I decided to let thing be until next week because the underneath and slab are nasty. Some of the volunteers/court workers will get things cleaned up so next week I can roll under it between the axles and feed the lines down and out of the capstan and route them to their respective places. Then the only other thing left is to locate and install a filter so the goo in the tank doesn't go thru the system, fill it and get the thing moving.
Oh yeah, gotta do the swing cylinder hoses, but those are "easy".
The last pic is of the "octopus" assembled and ready to install.
And my hair, what is left of it, and skin are silky soft, thanks to the oil bath I got when getting the -16 hoses pushed back so they could go up the center of the crane!
GIANT thanks to BLKHMMWV. Without his help, what happened today could not have been done. I love you man!
I'm tired.
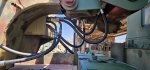
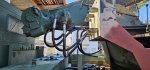
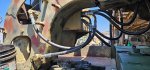
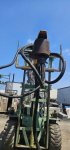
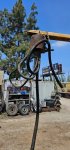
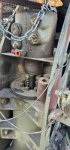
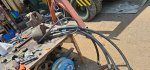