rtrask
Well-known member
- 342
- 251
- 63
- Location
- San Luis Valley, Colorado
I have had two frustrating days trying to remove the pistons from both of the stabilizers. The pins that attach the rod to the foot are seized on both sides, and nothing I have tried has budged them. Any ideas would be greatly appreciated. i will detail what I have done so far.
These are the steps I have taken:
Day 2.
At this point I decided I should replace the pins as they had both taken a real beating. I ordered two on Amazon so no point in trying to save them.
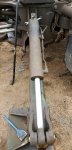
I can't understand how it could be so stiff. I never would have thought a rust weld on a working joint could be so strong.
Any ideas of what to do next?
These are the steps I have taken:
- On the right side, I removed the forward facing snap ring and tried to drive it back. It would not budge and the end started to mushroom so I removed the snap ring on the rear and tried to drive it forward. It moved about an eighth inch and I couldn't get it to budge either forward or back.
- I switched to the left side, removed the back side snap ring and attempted to drive it forward. it moved maybe a half inch and I could not get it to move forward or back. The pin started to mushroom.
- I went from a 5 lb sledge to an 8 lb sledge and tried it on both pins the only change was that it started mushrooming faster.
- I decided to focus on the left side since that seemed to have the most movement. I took a cold chisel and drove it between the rod eye, and rear mount
- I started liberally spraying penetrating oil and pounding the eye on the left side back and forth I would file down the ends to remove the mushrooming.
- Then I took a hydraulic jack and chain to put pressure on the pin and began smacking on top to try and shock it. Nothing (see attached picture)
Day 2.
At this point I decided I should replace the pins as they had both taken a real beating. I ordered two on Amazon so no point in trying to save them.
- Sticking with the left side I used my angle grinder and 7" cut off wheel and cut the pin on each side of the rod eye. I was able to pull the piston on the left side and drive the stub of the center portion out of the eye, but the outside portions are still unmovable.
- I don't have an acetylene torch, but I put 2 propane torches on the left rear mount for about an hour, and it made little to no difference in moving the stub on that side.
- I moved back to the right side, I wanted to use the chisel to get some space between the eye and rear mount, but no amount of beating on it would give me any separation to saw the pin on that side.
- I thought that possibly the cylinder being at an angle was putting a bind on the rod eye, so I disconnected the lines on that side, and drove the top pin out, but the cylinder will not move.
- I put a hi lift jack on the cylinder next to the mount, and jacked it out of the mount. It took a lot of pressure to do that, enough that I was really afraid of damaging the cylinder.
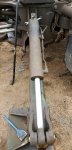
I can't understand how it could be so stiff. I never would have thought a rust weld on a working joint could be so strong.
Any ideas of what to do next?