springer1981
Well-known member
- 844
- 1,150
- 93
- Location
- Maine
I purchased 24v to 12v DC to DC converter at 20 amps to setup a 12vdc fused electrical system. I tapped off the CB-1 circuit breaker that runs the heater fan. Nothing on the 12v system will draw much current so it shouldn't be a problem if the heat fan is running. Also it's not really a winter vehicle for me so using the heat is a rare occurrence.
I mounted the DC to DC converter behind the kick panel by the drivers door. This put it out of sight and didn't use up valuable real estate under the dash. I ran it to a nice little 6 circuit fuse box. I mounted that using some good double sided tape because I didn't want to put any unnecessary holes in my fender.
After it was all mounted I connected TCU (Transmission Control Unit) to it and tested, worked great.
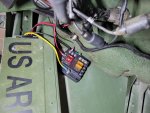
I mounted the DC to DC converter behind the kick panel by the drivers door. This put it out of sight and didn't use up valuable real estate under the dash. I ran it to a nice little 6 circuit fuse box. I mounted that using some good double sided tape because I didn't want to put any unnecessary holes in my fender.
After it was all mounted I connected TCU (Transmission Control Unit) to it and tested, worked great.
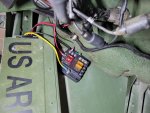