OK, so here are some images of what happened. First off, again, a giant shout out to
@BLK HMMWV . I could have not got things done without the help of him, his smaller than mine stature and perseverance. He is truly a motivated motivator. This hasn't been the first go round of him gently prodding me to just do what needs to be done and get it done and over with. I hope I have helped him out of tight spots as he helped me on this project.
Last week we got the swivel out, lines off, things cleaned up and new lines on. We capped the lines to prevent crud intrusion. Yesterday, this thing about kilt us both. We got the "new octopus" rigged up and got it into position. We tied some ropes to the lines so that they could be guided down the center into the correct cavities in the base of the capstan. Not an easy task even with lines that were MUCH more flexible. We also had to re-rig the spool so it could pivot. The upstairs was my job, Craig handled the forklift operation and BLK HUMMWV opted to go under the beast and guide things down. I don't think he planned to be where he was for the time he was there.
After a bit of wrestling, wiggling and prodding, the assembly went into the center of the capstan, a bit too far, so it needed to be pulled up to install the lock tabs and nuts....which reminds me, those nuts are not tight. I NEED to remember this!
Once the assembly was in place, I rolled under it to join my friend. It was nearly impossible to get the 2, -16 lines for the rotator cylinders onto the fittings they needed to be attached to. We ended up removing 2, 1/2 inch bolts that held a block for the supply/return to the bottom of the bed. After that, things went a bit more smoothly. These 2 lines took the two of us close to an hour to get attached, just those two lines! Not fun, covered in nasty, old OE10, grease, spider webs, no room under it, lights dying, etc. I will admit that I got VERY frustrated. Thankfully, someone was there to calm me down. Plus he said he wasn't gonna come back so we best get things done NOW!
After a bit of time, we got all of the swing and return lines connected, sealed and tightened. That was a work out!
I decided to leave the individual lines for the swing for today.
This morning, I started the assembly of all the lines in the operators area. I came across some issues with a couple of return lines. The return from the crane drum motor was apx 10 inched too short and the return from the valve body to the swivel was OK in length, but the length of the crimps didn't allow the line to bend/flex as it should to reach the fittings it needed to go to. A quick call to PirTek and a quick drive had that remedied. Got all of the lines from the valves to the swivel and the return lines installed, secured and ready to rock.
On to the swing cylinder lines. Oh He ll no! Those things are SO tight! It takes a 7/8 wrench on the fitting that is threaded into the block that we had a tough time getting the -16 lines onto. I put a 24 inch long wrench onto the 7/8 wrench to try and break those lines loose. Seems the same jack azz that installed every other line on this, installed these. I was doing a pull up on the wrench! No room for a hammer. Just decided to leave those. They have been covered and don't look too bad. IF something happens, I'll just cut the lines at the hex and impact them out.
We want to install some sort of filter on the suction side. I took the cover off of the tank. There is a tapered fitting that sticks up 3 inches or so off the bottom of the tank. It almost looks like thee could have been some sort of filter pushed onto that taper. I can find nothing in the books on the tank. Anyone have a clue if the is a filter that should be there?
The last picture is of the four lines that I couldn't get loose.
I am tired!
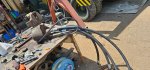
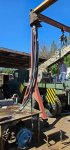
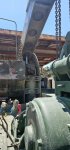
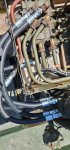
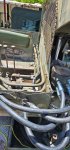
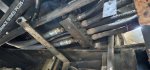
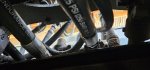
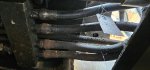